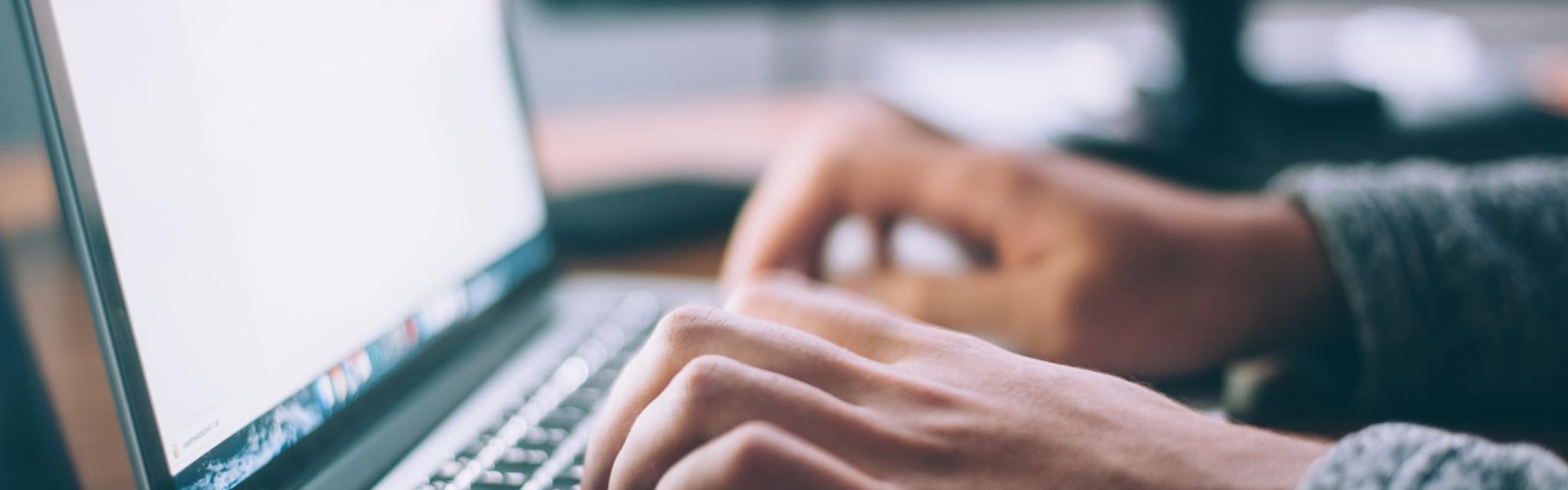
While the first part of this article emphasized on metallurgical aspects occurring in laser melting and their underlying factors, this second part investigates more deeply about the specific nature and dependence of the mechanical properties obtained in metal additive manufacturing (ALM).
Appropriate structural organization offers higher mechanical properties…
Mechanical properties obviously depend on the type of material considered but also on the part density, and how the internal crystal or “microstructure” forms.
From a macroscopic standpoint, ultimate tensile strength and elongation generally increase with the final density but the effect is different for each powder. Particle size -more exactly pore size - has a significant influence on mechanical properties. Indeed, pores can be regarded as defects that reduce the effective cross-section. Basically, mechanical properties are degraded as porosity and pores size increase.
From a closer standpoint, the laser beam melting usually forms very fine grains because the high cooling rate prevents them to grow further. Depending on the composition of the powder, non-equilibrium (metastable) phases and new chemical compounds may appear.
Such microstructural configuration results from the short exposure period of the laser irradiation. It gives rise to fully dense printed parts with mechanical and physical properties as good as or better than those of comparable wrought or cast materials. A slight increase in strength and decrease in ductility is usually expected because of ALM's refined grains, but it depends on post heat treatment and test direction.
A good first indication of resistance to deformation is obtained through hardness measurement. Afterwards, tensile tests are recommended on normalized samples to get precise properties such as ultimate tensile strength and elastic limit (yield strength).
Despite slightly anisotropic…
A certain degree of anisotropy in mechanical properties is caused by the layer-by-layer approach. The tensile strength measured in the build direction is slightly lower than in the XY-plane.
Anisotropy can be mitigated either after build by an appropriate thermal treatment, either before with a proper laser scanning strategy. Compared with conventional scanning strategies (layers with unidirectional vectors or cross-ply pattern), some rotation from a layer to another leads to better overlapping and less anisotropic properties.
Relieve thermal stresses by post-processing a heat-treatment…
When a part is additively manufactured, each layer or volume of material presents a complex thermal history. It may involve several cycles of re-melting, re-solidification as well as multiple solid state phase transformations. Combined with the high heat transfer rates attributable to "powder-bed" ALM processes, post-built parts naturally contain high residual thermal stresses that can distort geometry.
From a preventive perspective, the level of residual stresses is dependant upon the material and build parameters. Moreover, to improve dimensional stability, a stress-relief annealing can be performed before removing parts from their platform (300°C during 2 hours to AlSiMg, for example).
… And if the material is suitable, why not age hardening?
Hardness (thus ultimate tensile strength) achieved with ALM is usually higher than that of conventionally produced parts due to the natural aging phenomenon which occurs throughout the melting and re-melting of every layer.
Depending on the metal, a further age (or precipitation) hardening heat treatment can increase the ultimate tensile strength. While not always, hardening is often a trade-off, at the expense of ductility (elongation at break will be reduced).
To undergo precipitation strengthening, an alloy must possess aging constituents that can be dissolved (solid solubility) during the "solution annealing" and then be precipitated into the metal matrix during the "age hardening".
Different aging times and temperatures can be tested to find out a proper combination (5 hours at 480°C for maraging steel 300, for example), because at a prolonged times, material properties may deteriorate due to "over-aging".
For fatigue resistance, shot peening is performed…
Shot-peening is a surface treatment where small balls impact on the part to induce compressive residual stress at the surface and slightly below. The sub-surface compressive residual stress field delays crack initiation and thus, postpones crack propagation.
Shot-peening method should be optimized to improve depth of compressive residual stress field while minimizing surface roughness.
A consistent quality inspection…
To ensure the quality of the production and maintain precise specifications, Spartacus3D manufactures specimens to conduct an assortment of materials testing operations such as:
- Metallurgical / microstructure analysis
- Chemical analysis
- Mechanical testing
The following picture present a set of testing samples for metallurgical or microstructure characterization:
This experimental approach allows Spartacus3D to validate the key mechanical properties claimed by machines and powder materials manufacturers within their datasheets.