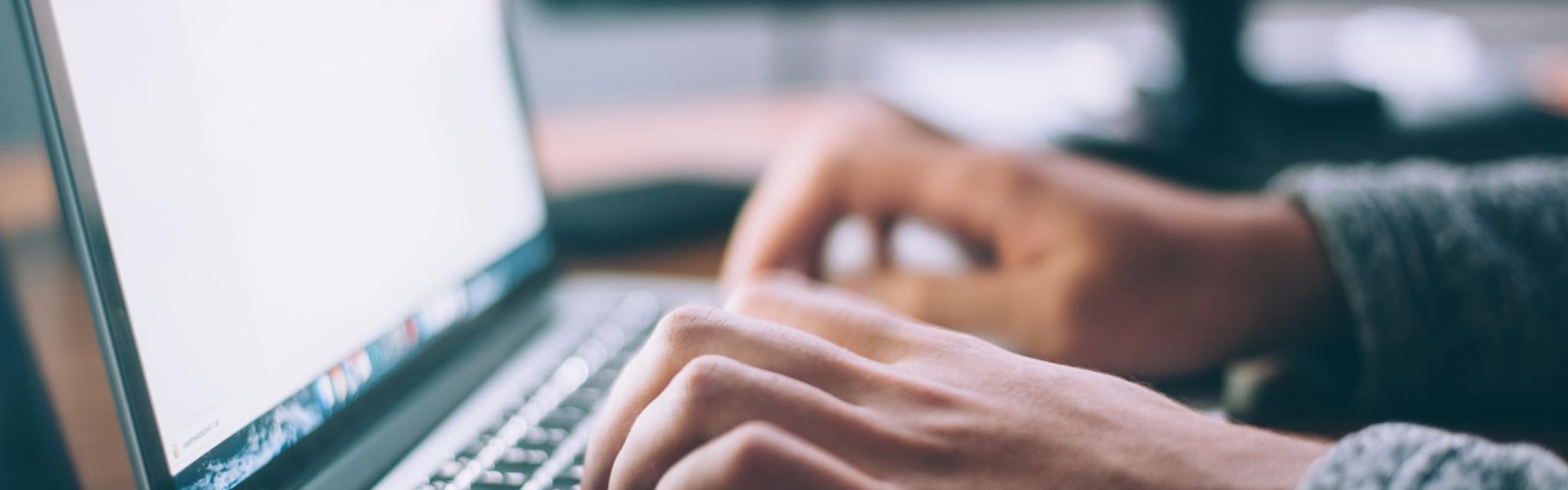
The roots of laser-aided metal additive manufacturing lie in 1977s with the general principle patented by Russ Householder, a private inventor. He described a system and method which bore an uncanny resemblance to future commercial laser-aided powder-bed systems.
The commercial history started in the early 1990s. Several firms and institutes have participated in the development of the technology and some companies were bought or fall out along the way. Nowadays, different names refer to the same technology because of a tortuous marketing path and several patent issues.
Acronyms SLM and DMLS are somehow remnants from a period that precedes the entry into cooperation of the main actors and patent cross-license agreements that granted them licenses to their patent portfolios. Before that, both techniques were formerly distinct in their ability to either fully melt (SLM) powders particles or sinter them (DMLS) whether it was pure components (pure titanium or aluminium) with a single melting point or pre-alloyed powders (stainless steels, super-alloys and Ti64, for example). Today, SLM is also used for ALM of pre-alloyed metals and merely a synonym of DMLS.
Moreover, while SLS (or LS) used to describe the process as applied to a variety of materials (metals, plastics, glass, ceramics), it is now generally used for laser sintering of plastics.
What are the Metal ALM Processes and Machine Providers?
Metal additive manufacturing processes and systems providers.
Powder-Bed Fusion Systems
The additive manufacturing processes in which powder particles of particular regions of a powder bed are selectively fused together by thermal energy.
Selective Laser Beam Melting Systems
The most widely used systems. In DMLS, layer thicknesses usually range from 20 µm to 60 µm. The process builds objects by distributing even layers of metallic powder with a recoater, then melting each layer with a laser under an inert atmosphere. The powder feedstock suitable for DMLS presents a particle size typically distributed between 10-50 µm.
Metal parts produced by DMLS (Spartacus3D).
The scanning velocity and layer thickness are limited by the available laser power and the behavior of the material during the melting process. The hatch distance is limited by the diameter of focused laser beam to be same as the beam diameter in order to achieve pore free structure. DMLS’s repeatability is about 20 µm in all directions and the minimum detail resolution about 100 µm in the plan and 20 µm in the build direction.
Selective electron beam Melting systems
Who are the main providers for power-bed metal ALM systems?
- EOS (Germany), Direct Metal Laser Sintering (DMLS)
- 3D Systems (USA), Direct Metal Sintering (DMS)
- SLM Solutions (Germany), Selective Laser Melting (SLM)
- Realizer (Germany), Selective Laser Melting (SLM)
- Concept Laser (Germany), LaserCusing (LC)
- Renishaw (UK), Selective Laser Melting (SLM)
- Arcam (Sweden), Electron Beam Melting (EBM)
- Wuhan Binhu (China), Selective Laser Melting (SLM)
- Huake 3D (China), Selective Laser Melting (SLM)
Directed Energy deposition systems
The additive manufacturing processes in which material is fused as it is deposited, by the means of focused thermal energy.
Directed Energy Deposition is a blanket name that encompasses many deposition techniques:
- Direct Metal Deposition (DMD)
- Direct Laser Deposition (DLD)
- Laser Deposition Technology (LDT)
- Laser Additive Manufacturing (LAM)
- Laser Metal Deposition (LMD)
- Laser Engineering Net Shaping (LENS)
- Laser Cladding Technology (LCT)
- Laser Freeform Manufacturing Technology (LFMT)
The Process Behind The Blanket Name
The process employs a directed energy source (laser usually, but also electron beam) to create a metallurgical bond between a cladded material and a product’s base material, under tightly controlled atmospheric conditions. A typical DED machine consists of a nozzle mounted on a multi axis arm, in which a focused energy beam melts the surface of the target material to create a small molten pool of base material. The processed material can be either powder-blown (powder-fed) or wire-fed, and is deposited within the spot to be absorbed into the melt pool.
The deposit’s dimensions are ranging from 15 to 100 µm in thickness and from 0.1 to 0.4 mm in width. The technique can be used to produce entire 3D parts or repair components cost effectively by cladding material in thin layers to restore the worn surface.
Who Are The Main Providers For Directed Energy Deposition Systems?
The main companies that are currently developping proprietary technologies based on this process and marketing solutions are:
- BEAM (French), Construction Laser Additive Directe (CLAD) process and MAGIC machine (LMD/Cladding).
- Optomec (USA), Laser Engineered Net Shaping (LENS) process, 850-R machine and modular Print Engine.
- Sciaky (USA), Electron Beam Direct Manufacturing (EBDM) process (wire-fed) and VX-110 system.
A Technique Remarkably Suitable For Hybridization With Traditional CNC Machining
Directed energy deposition is being developped in the context of hybrid machines. To conventional CNC milling capabilities, are associated the additive manufacturing capabilities of blown-powder processes, either as turnkey system configurations or as modular docking systems embeddable into existing CNC machine tools.
The flexibility to change at any moment between directed energy deposition and milling allows the machining of sections that are not normally reachable within a standard 3D printed part (after-built) and attain, through finishing, surface qualities that can’t be obtained in powder-bed ALM systems.
As the hybrization is still nascent, a very few companies are driving the industrial development of hybrid manufacturing solutions using directed energy deposition:
- DMG Mori (Japan), LASERTEC 65 3D, hybrid AM/Milling machine.
- Hermle (Germany), MPA 40 3D, hybrid AM/Milling machine.
- Hybrid Manufacturing Technologies (UK), AMBIT modular docking system for CNC machines.
Comparison of powder-bed additive manufacturing systems for industrial production
An industrial printer’s features (resolution, surface finishing, build platform size, variety of materials and flexibility for switching from one to another, additive manufacturing method, etc…) must be balanced with the needs of the production line (printing prototypes quickly or accurate parts for end-users, tooling equipment, applied research, etc…).
Typically, the main metal production 3D-printers are capable of printing high-grade steels, aluminium, nickel-base and titanium alloys and pure titanium.
Several production 3D-printers from the main providers.
Market trends in laser-aided industrial printers
Extended offerings are marketed to answer new customer needs, which follow up the penetration of the technology within the industry and its improvements. Upmarket models present upgrades in terms of capacity, accuracy, productivity (speed) and ergonomics such as:
- Larger build area to cram up as many individual parts as possible or open up the process to larger applications.
- Enhanced aptitude for printing different materials.
- Supersize machine dimensions to include productivity-enhancing modular set up (removable build chamber with offline setup, powder preparation facility, post-print booth) and get new parts printing in the machine without any delay.
- Multi-laser system to speed up the production.
- Reduction of operating costs due to lack of expensive wear and tear on machine parts.
- Automatic recirculating powder handling.
- Self-cleaning filter units.
- Centralized cooling station.
- Improved Control System & Software.
- Recycling external system.
- Automated loading system.
Spartacus3D follows the latest technology trends in additive manufacturing, in order to be one step ahead and apply the best solutions for its customers.