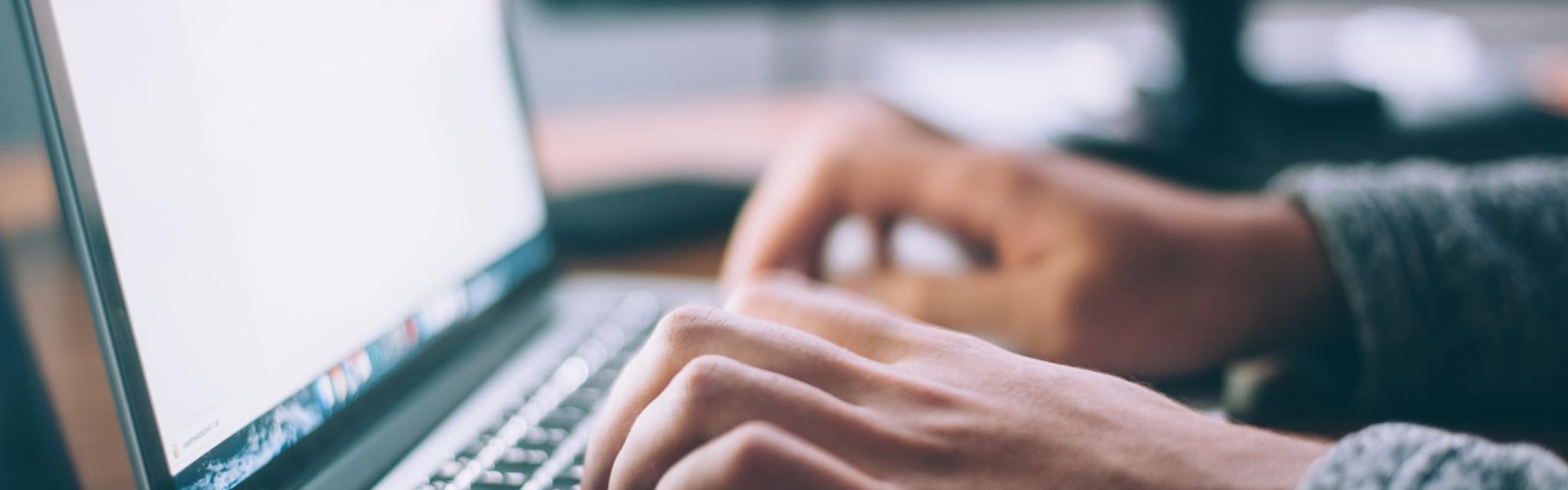
Modern aircraft engines are far more reliable than their predecessors because of great strides in technology. Truer now than ever, design is driven by fuel efficiency and reliability. Engines can stay on wings for years and a single pair suffices to power large jetliners across oceans. Beside commercial applications, mission-critical defense operations increasingly rely on the peak performance the engines offer.
Further improvements are coming with the rising interest of aerospace industry towards additive layer manufacturing (ALM) of ever more critical components. To reap the best costs and performance benefits from metal ALM, aerospace applications focus on complex components made of high-value materials such as Ti6Al4V or Inconel 718.
Super-Alloys, A Class Of Material For Stringent Applications
Hotter is the combusion, more energy efficient is the engine
Carnot said that operating engines hotter improves energy efficiency, thereby, fuel efficiency. To do so, aerospace engineers rely on super-alloys for the hot sections of turboreactors. Also known as "heat-resistant super-alloys" or "high-temperature alloys", they can withstand severe mechanical stresses and strains in extreme environments while remaining stable, corrosion and creep resistant.
Super-alloys endure extreme conditions
Nickel-iron based super-alloys are particularly well suited for service in high-temperature environment where creep, corrosion and thermal shock resistances are desired. Generally, they can be hardened by solid solution strengthening or precipitation of intermetallic compounds within the metal matrix.
Inconel 718, The Workhorse Of Super-Alloys And Keystone Of Hot Structural Aerospace Applications
Introduced in 1965 at industrial scale, Inconel 718 is relatively recent but extensively used nowadays.
The predominant super-alloy in the world
It represents about half of their world tonnage and is considered as a refractory super-alloy since it can be used permanently above 600°C. Its Young's modulus is almost twice that of Ti6Al4V and similar to that of an unalloyed hardenable carbon steel (CK 45).
The alloy associates good creep and rupture strength with a high resistance to fatigue. It possesses long time strength and toughness at higher temperature along with confinement of corrosion resistance up to high temperature.
... and in turbofan jet engines
Inconel 718 accounts for up to 50% of the weight of aircraft turbojet engines, being the main component for discs, blades and casing of the high pressure section of the compressor and discs as well as some blades of the turbine section. It also finds several applications in rocket engines and cryogenic environments due to its good toughness at low temperature (preserving parts from a brittle fracture).
Chemical composition of Inconel 718 (%-weight).
Thanks to its high Iron content, but not only...
Inconel 718 contains significant amounts of Iron, lowering its price per kilogram while endowing it with precipitation hardening effect. Iron's low mobility in the matrix confers the main strengthening phase (γ’’) a sluggish precipitation kinetics that reduces susceptibility to post-weld cracking. Indeed, Inconel 718 was designed to overcome the low weldability of this class of materials, generally susceptible to cracks (microstructural segregation of alloying elements in the heat-affected zone of welds).
Specific alloying elements give Inconel 718 a strong resistance to corrosion up to 1000°C. For instance, Nickel is useful in combating chloride-ion stress-corrosion cracking and protects from corrosion in many inorganic and organic oxidizing compounds, in a wide range of acidity and alkalinity. Chromium imparts an ability to withstand attacks from oxidizing media and sulfur compounds while Molybdenum is known to improve resistance to pitting corrosion.
Inconel 718, Customizable Mechanical Properties
Moreover, as other nickel-iron based super-alloys, Inconel 718 can be hardened. It is desirable for structural components operating at high temperatures.
Heat-treatements unleash its potential...
Two strengthening modes are combined: solid solution hardening (atoms of iron, chromium, molybdenum and niobium can substitute to nickel within the metallic matrix) and hardening by a precipitation of ordered intermetallic phases, γ' and γ'’.
Titanium and Aluminum form by precipitation the intermetallic phase γ', Ni3(Ti, Al), metastable and hardenable again by solid solution of Niobium and Titanium (at room temperature) and of Tungsten or Molybdenum (at high temperature).
At a temperature close to 650°C, Niobium combines to Nickel to form by precipitation the γ'' phase (Ni3Nb), which has very high mechanical properties at very low and moderately high temperatures. Although γ´ and γ’’ are present in the aged condition, the amount of γ´ is much lower and γ’’ is recognized as the primary strengthening agent. γ’’ precipitates are disk-shaped, with a thickness of 5-9 nm and an average diameter of roughly 60 nm.
The next structural components are primary carbides (created by elements such as Cr and Ti) and secondary carbides (created by elements such as Cr, Co, Mo and W). However, except of these structural components, undesirable phases can also appear.
Material properties tightly adjusted for more performance
Influence of precipitates on hardness can be felt only if they reach a critical size to affect the dislocation movement. Which phases are generated and in which amount, the shape and size of these structural components have a significant influence on final the mechanical properties of alloys and mainly on creep rupture life.
Inconel 718 must be first annealed to ensure the aging constituents (Aluminum, Titanium and Niobium) are dissolved in the matrix. If already combined, they won’t properly precipitate and realize the optimal hardness of the alloy.
Every Material Has Limitations. For inconel 718.... 650°C !
When stress and creep resistance are expected, applications are restricted below 650°C because γ′′, meta-stable, rapidly overages under a prolonged exposure at or above this temperature. A rapid coarsening of γ′′, solutioning of both γ´ and γ′′ and microstructural shift, from the coherent disk-like γ′′ phase to the stable, plate-like δ phase of Ni3Nb, followed by a loss of strength and especially creep life.
Temperature dependence of mechanical properties for the aged Inconel 718.
Inconel 718, Flip side of excellence: a very Challenging machining
Hot machining slightly facilitates to shape the material!
The high strength, toughness and work hardening of Inconel 718 lead to high forming loads for room temperature fabrication which may cause manufacturing difficulties. For convenience, Inconel 718 can be machined at temperatures exceeding 540˚C.
Machining complex parts involve costly tools and material losses
The forming problems combined with the complex geometries typically required in aerospace applications, result in components that are often difficult and costly to manufacture. During machining, very high temperature is attained on the cutting edge of the insert due to the low thermal conductivity of the alloy and abrasive elements in its material composition. It encourages high wear rates, chipping, notching and cutting edge breakage.
The work hardening after the first machining pass tends to plastically deform either the workpiece or the tool on subsequent passes. Generally, most material is machined away when the workpiece is in the solution annealed form (softer material) and only the finishing steps follow the age hardening. A slow but aggressive cut is used with a hard tool to minimize the number of passes required.
Not only the cutting tools life is shortened, but parts also tend to warp because of the metallurgical sensitivity to residual stresses and self-hardening effects during machining.
Inconel 718, also a Limited Aptitude For Investment Casting
The high mechanical strength and hardness of Inconel 718 limit its formability, even at hot temperature.
For lack of a better way, components have often been casted
Consequently, most of Inconel 718 parts are produced by investment casting. Compared to other traditional metal processing methods, it allows an improved material usage (“buy to fly”), the ability to produce relatively complex configurations at a reduced cost.
However, investment casting can be disadvantageous due to Inconel 718’s susceptibility to metallurgical defects such as porosity, segregation and very coarse grain sizes, which reduces functionability and calls for subsequent processing steps, adding cost to finished components. For non-structural applications, it is used in the cast and heat treated condition but for structural applications, investment cast Inconel 718 is frequently hot isostatically pressed (HIP) to minimize shrinkage porosity and casting segregation.
But it's by no means perfect!
Another concern with investment casting of Inconel 718 is that zones of local segregation (typically Niobium) produce regions of high local hardness during heat treatment. These regions favor an increased tool wear and occasional catastrophic tool failure and concomitant increased manufacturing cost (for deviant or scrap parts in the case of tool failure).
Why additively manufactured Inconel 718 Benefits Aerospace Applications?
Traditional manufacturing methods are challenging when applied to Inconel 718 and one often ends up sacrificing the excellent material properties (high temperature corrosion and creep resistance) to obtain the desired shapes. Machining, forging and welding also require the material being preliminary annealed to induce ductility and better deformability.
ALM doesn't sacrifices 718's excellent mechanical properties
In contrast, metal additive layer manufacturing (DMLS/SLM) makes Inconel 718’s processing more convenient, straightforward and ensures material properties are well preserved. ALM Inconel 718 has demonstrated directional solidification, which has been shown to equate or exceed mechanical properties of cast and wrought counterparts.
ALM stimulates creativity to improve performance...
Additionally, ALM brings aerospace engineers more design freedom to deal with complexity. They can incorporate internal and external features simultaneously from the ground up, consolidate an assembly into fewer parts to reduce downstream operations and push light-weighting of parts to the limits by lattice-structuring design. ALM also frees more time for quality assurance of high-end functional parts.
ALM produces almost no material wastes of expensive superalloys!
Last but not least, milling of aircraft parts results in high rate of recyclable waste. With layer-wise building of components with near-final contours, the process produces only about 5% waste, improving the “buy-to-fly” ratio of aerospace components.
Spartacus3D understands the importance of Inconel 718 for high-end aerospace applications and aims to release the power of metal ALM in response to this industry’s focus on higher performance, reliability and lower costs.