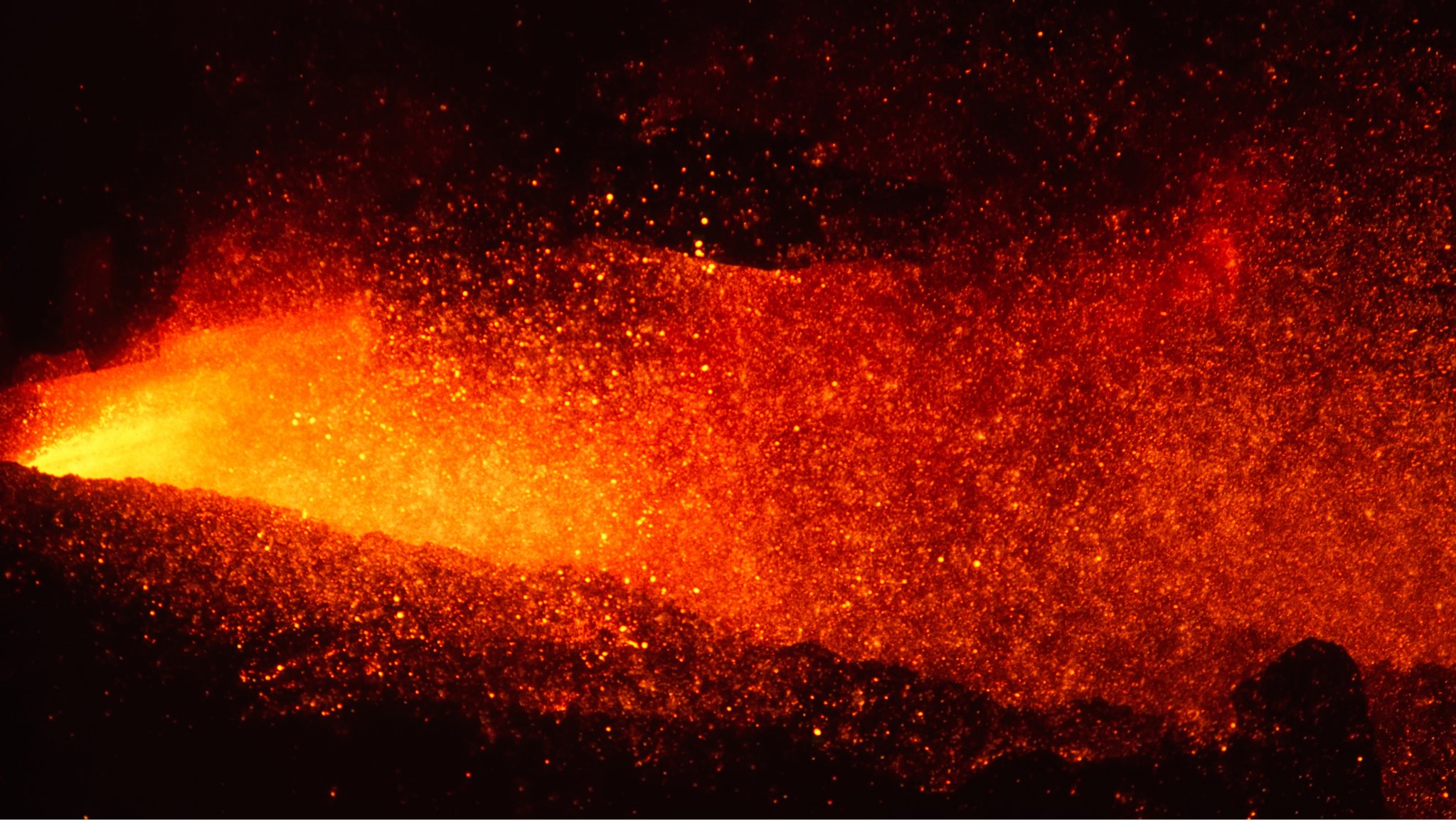
FOUNDRY PROCESS
FMGC is a recognized specialist in the casting of counterweights and ballast solutions for all sectors of activity: public works, handling, agriculture, navigation, EMR, Oil & Gas.
A RIGOROUS INDUSTRIAL process
The foundry process makes it possible to obtain, by molding and melting metals, parts of varied and complex shapes.
At FMGC, this process uses GL cast iron (lamellar graphite), a high density material (7.1) that has many qualities: ease of machining, excellent corrosion resistance, mechanical characteristics in line with applications, and dimensional stability.
Particularly suitable for components with complex shapes, the foundry also allows for high repeatability and therefore for both mass production and customization.

Production and characteristics
Casting
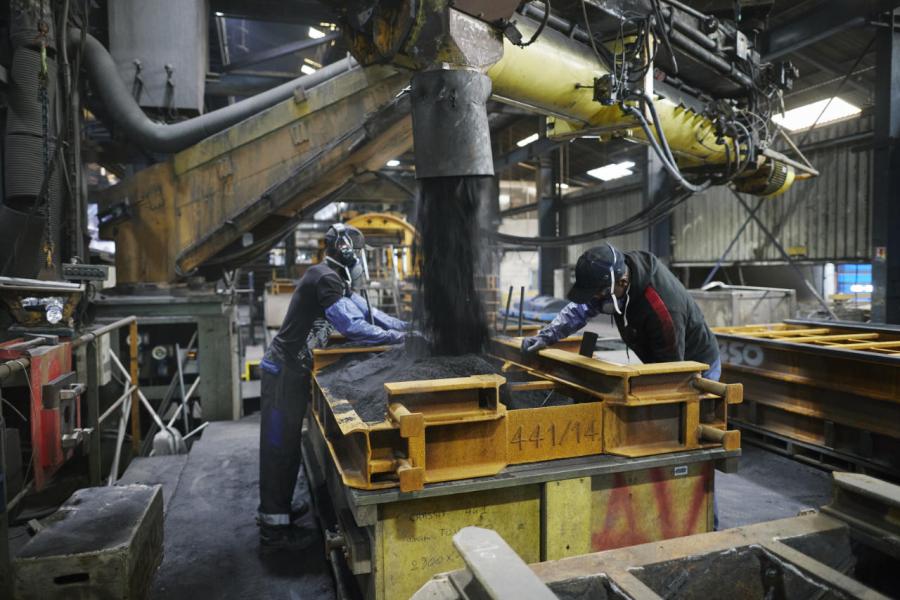
This is the first step in the casting process.
Thanks to dedicated tools, a sand mold is made, reproducing the shape of the part to be obtained.
Melting
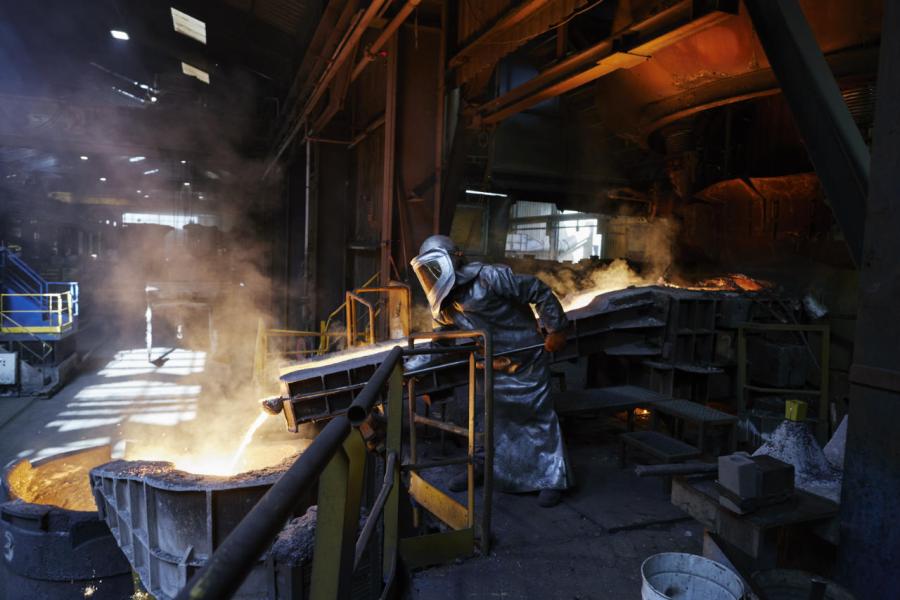
The liquid iron, melting between 1200 and 1500 degrees, is poured into the mold. The chemical composition and the casting temperature of the metal are two key parameters, controlled at FMGC by state-of-the-art control equipment (spectrometer, supervision, pyrometric rod).
After a cooling period, the mold is opened and the extracted part is put in final cooling.
Deburringand finishing
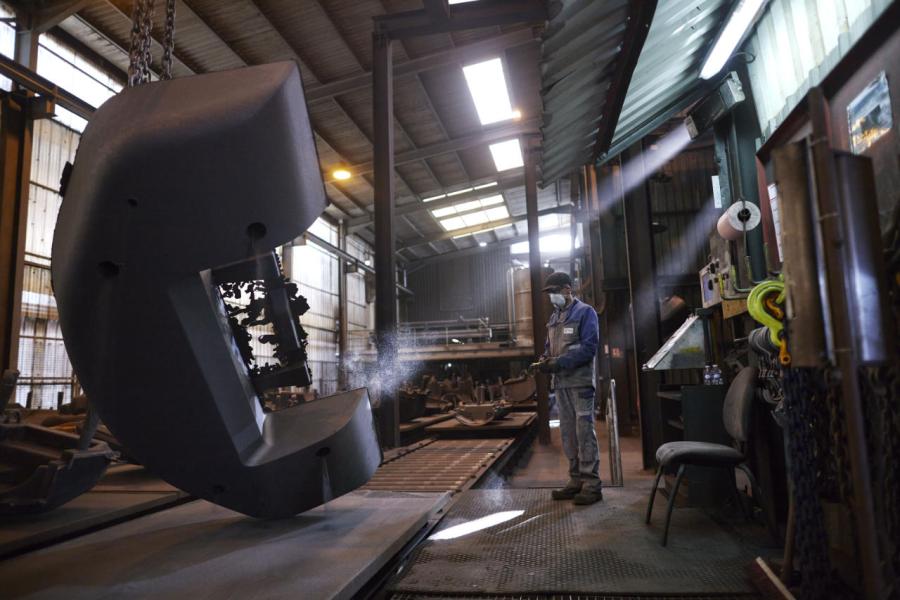
Once cooled, the part is shot-blasted with steel balls to remove the remaining sand.
It is then deburred by robot: the metal burrs that have appeared between the two parts of the mold are removed by grinding. Particular attention is paid to dimensional checks.
The component is then sanded and primed before being painted. Numerous possibilities of personalized finishes are proposed on request (lacquered or structured paint, wide range of colors).
Machining

To meet specific customer requirements depending on the desired final product (compactness, precision assembly, better integration of parts, functional capacities, etc.), various precision machining operations can be performed on the finished part during the casting process: drilling, tapping, surfacing, etc.
At FMGC, these operations are particularly advanced. They are performed on specifically designed numerical control machines, developed with our suppliers and installed in dedicated buildings.
FMGC'S CONTROL OF MATERIALS
Active participation in the recycling of materials
The raw materials used in the foundry come from recycling and reuse circuits. They are recovered cast iron and steel parts, sorted, calibrated and controlled according to strict specifications.
To further strengthen the virtuous impact of this process, which contributes to the circular economy, FMGC favors regional sourcing.
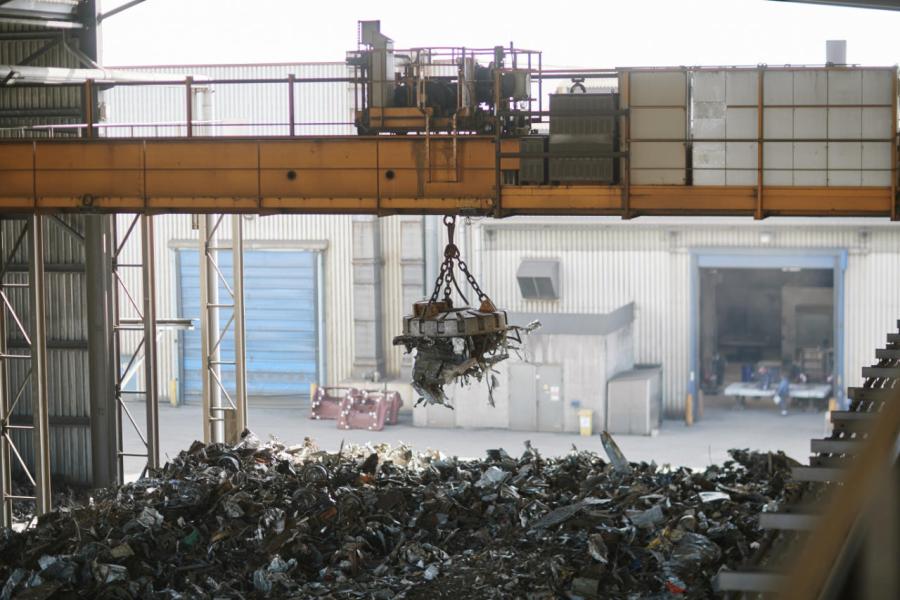
A perfect control of the process, for a high quality material
FMGC produces EN-GJL cast iron with a density of 7.1, meeting the DIN EN 1561 standard.
Thanks to its perfect mastery of processes, its state-of-the-art equipment managed by experienced teams, its high level of control, its purchasing policy and its high level of investment (5 to 7% of annual turnover reinvested in R&D), FMGC is recognized for the quality, regularity and reliability of its production.
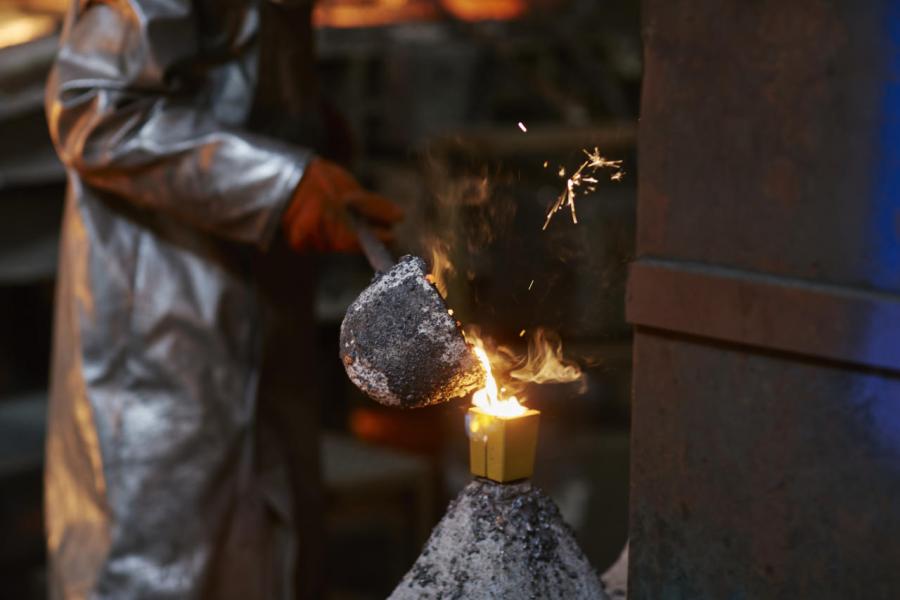
Our expertise in this field could make the difference in the success of your project
FMGC process and equipment
- 2 production lines: semi-automated small and medium parts molding and large parts molding
- Melting tool: 1 hot blast cupola 25T/h
- A deburring robot
Machining
- 6 machines
- 1 Corréa machine
- 1 FPT machine
Quality and control
- Monitoring at each stage of the process (molding / melting / finishing / machining / shipping)
- High performance control equipment (spectrometer / 3D scan / internal laboratory / supervision and digital control of the melting tool)
Smart Factory
- Collaborative project management and monitoring software developed in-house
- CMMS software deployed throughout the site
- Monitoring and sensor on key equipment
Sustainable development
- Water-based refractory coating instead of alcohol-based solutions
- 95% recycled molding sand
- Heat recovery from cupola furnace (melting tool)
Read more
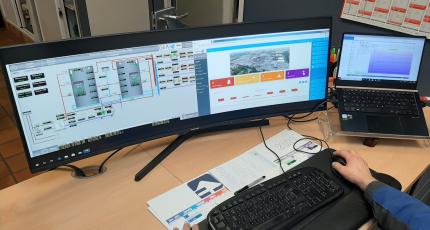
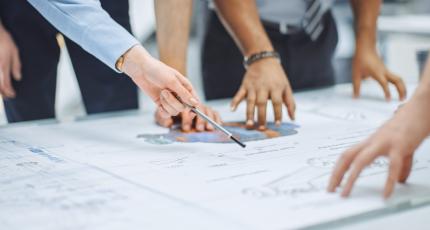