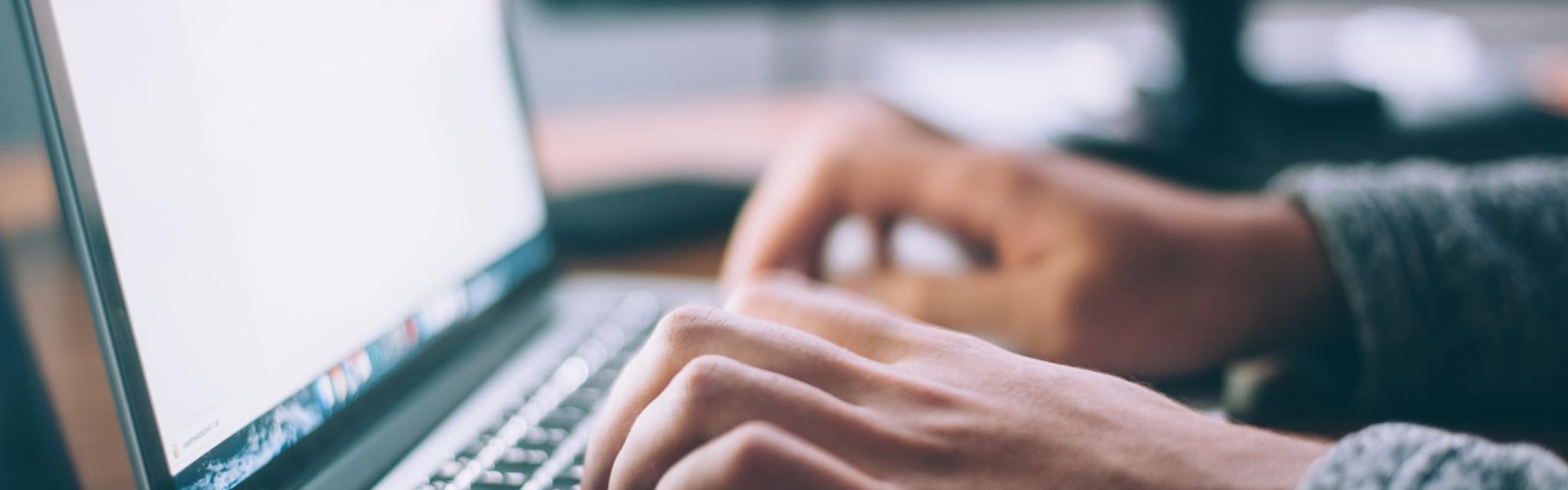
Principales considérations, matériaux et applications
Il existe trois types de procédés de forgeage, qui varient en fonction de la température : à chaud, mi-chaud, et à froid. Bien que le forgeage à chaud soit la technique de production la plus ancienne, le choix de l’une de ces techniques ne repose pas seulement sur leur qualité, mais sur les caractéristiques voulues pour le produit final, ainsi que sur l’optimisation des coûts de production en fonction de la taille de la série produite. La forge permet d’affiner la structure granulaire du matériau, principalement des métaux et alliages, et permet ainsi d’améliorer les propriétés mécaniques du composant pour renforcer sa solidité. Des presses et pilons complexes sont utilisés pour déformer les matériaux et obtenir la forme souhaitée.
Forge à froid vs. forge à chaud : explications, avantages et inconvénients
Description du procédé
Le procédé de forgeage à chaud est réalisé à la plus haute température qui ne détruise pas les propriétés métallurgiques de l’alliage utilisé (jusqu’à 1250° pour l’acier, de 300° à 460° pour les alliages d’aluminium, de 750° à 1040° pour les alliages de titane et de 700° à 800° pour les alliages de cuivre).
La recristallisation se produit en même temps que la déformation, pour éviter ainsi l’écrouissage. C’est pour cette raison, et pour obtenir le meilleur résultat possible, que la température doit être maintenue tout le long du procédé au dessus d’une température minimale spécifique, propre à chaque alliage. Ce traitement du métal permet d’obtenir une bonne forgeabilité et ainsi d’éviter les criques, car la ductilité peut être sévèrement réduite à des températures plus faibles. L’étape de forgeage doit donc être assez limitée dans le temps afin de limiter les variations de température.
Si le forgeage n’est pas fini au moment où la température atteint cette limite, il sera nécessaire de réchauffer la pièce pour une 2ème chaude de forge lorsque cela est possible (certaines lignes ne permettent que de chauffer des lopins par induction, généralement pour les grandes séries), sans quoi la pièce sera considérée comme étant « forgée », c’est à dire finie. L’intervalle de température nécessaire pour le procédé de forgeage à chaud est tellement essentiel que tous les outils doivent être pré-chauffés afin de limiter les baisses de température au niveau du composant lors de l’étape de forgeage. C’est ainsi qu’a été mis au point un procédé très précis et spécifique pour la fabrication de forge à chaud en matrices fermées (estampage ou matriçage) appelé « forgeage isotherme ».
Durant le forgeage isotherme, les outils (matrices) sont maintenus à la température nominale de forgeage. Le concept varie cependant selon le matériau utilisé, dont dépend également la température de forgeage. Les gammes de matériaux utilisées pour les matrices doivent leur permettre de conserver, à la température de forge, les propriétés mécaniques nécessaires pour déformer le matériau du composant sans qu’elles ne se déforment elles-mêmes.
Quelques exemples de forgeage isotherme appliqué à différents matériaux :
- Cette technique est obligatoire pour le forgeage de l’aluminium, car ce matériau refroidit très rapidement et sa température de forgeage est assez basse : toutes les nuances d’acier à matrices sont capables de maintenir les propriétés mécaniques requises.
- Cette technique est envisageable pour les alliages de cuivre et de titane, si des nuances d’acier à matrices très élaborées et coûteuses sont utilisées.
- Cette technique est très difficile à appliquer aux alliages d'acier, car très peu de matériaux de matrices (tels que le molybdène pur) sont capables de supporter les contraintes liées au forgeage à 1250°.
Ainsi, le forgeage isotherme est assez inhabituel pour les alliages de titane, et reste très rare pour les alliages d’acier et de nickel (par exemple pour les disques de turbine pour moteurs aéronautiques (réacteurs et turboprop).
Setforge propose des procédés de forgeage isotherme de qualité pour les alliages d’aluminium .
Afin d’éviter la contamination par des gaz durant le procédé de forgeage à chaud (contamination à l’O2, au H2 ou encore au N2), il est possible de protéger le composant d’un revêtement ou grâce à une atmosphère contrôlée (gaz inerte) à l’intérieur du four, du chauffage par induction et même au niveau de la presse.
Un lingot en métal forgé ou une pièce métallique moulée est compressé par des matrices, qui « cassent » sa structure granulaire. On obtient ainsi un grain plus fin et plus homogène, qui permet d’améliorer l’élasticité et la ductilité du matériau. Le métal étant chaud, il est facile à déformer, et cela permet ainsi aux fabricants de créer des formes plus élaborées qu’avec le forgeage à froid. Le métal est déformé au dessus de sa température de cristallisation, ce qui lui permet de conserver la forme qui a lui a été donnée au moment lors du refroidissement. Le façonnage est suivi du refroidissement, qui constitue une étape essentielle : en effet, un refroidissement trop rapide de pièces forgées à chaud peut provoquer un gauchissement de la pièce.
Avantages principaux
Le procédé de forge à chaud permet de produire des formes plus variées qu’avec d’autres procédés de forge. De plus, les matrices n’étant pas chères à produire (comparé au coût des outillages de forge à mi-chaud ou à froid), ce procédé est particulièrement adapté à la production de petites quantités et de composants bien proportionnés. En réalité, les autres procédés (forgeage à mi-chaud et à froid) sont conçus pour d’importants volumes de production, à destination de secteurs tels que l'automobile, ou pour produire des composants à géométrie simple pour lesquelles des matrices extrêmement complexes peuvent être conçues et amorties grâce au grand nombre de pièces produites.
Principaux inconvénients de la forge à chaud
Les parties fonctionnelles du composant doivent être usinées avant l’assemblage, car l’état de surface, la tolérance dimensionnelle et la contamination résiduelle de la surface ne permettent pas de concevoir un assemblage mécanique habituel.
Le rendement matière (rapport entre le poids du lopin engagé et de la pièce finie, appelé mise au mille dans le métier) est également plus élevé qu’avec le forgeage à mi-chaud et à froid à cause de la calamine (oxydes métalliques) formée pendant la chauffe de forge puis durant le traitement thermique, et de l’usinage qui suit.
Quels sont les principaux éléments à prendre en compte ?
Refroidissement
Comme dit précédemment, le refroidissement doit être mené avec beaucoup de précaution pour éviter les risques de gauchissement.
Tolérance
Il est également important de souligner que le forgeage à chaud offre une tolérance dimensionnelle moins précise que le forgeage à froid.
Bavure (matière sortie par le plan de joint séparant les matrices)
Il existe deux types de forgeage à chaud : avec ou sans bavure (matière sortie par le plan de joint séparant les matrices). Le premier est destiné aux pièces d’une géométrie complexe, en 3D, alors que le second est généralement limité à des composants axisymétriques et aux géométries cycliques et symétriques.
Matrices
Les matrices utilisées pour le forgeage à chaud sont faites sur mesure afin de correspondre aux conceptions des clients. Le procédé est réalisé au moyen de pilons à contre-frappe, simple effet ou double effet, de presses à vis ou hydrauliques, et d’autres machines dont le but est de compresser le matériau chauffé pour obtenir la forme souhaitée.
Les matrices utilisées pour le forgeage à chaud subissent plusieurs cycles thermiques et charges mécaniques, c’est la raison pour laquelle il est nécessaire de prendre en compte la déformation plastique, ainsi que les fissures et l’usure dues à la fatigue thermique. Pour prolonger la durée de vie des matrices, une bonne ductilité et un bon niveau de dureté et de résistance sont indispensables.
Quels sont meilleurs matériaux pour le forgeage à chaud ?
Le forgeage à chaud peut être utilisé pour fabriquer un large éventail de pièces, et il est ainsi possible d’utiliser la plupart des alliages ferreux et non ferreux, tels que :
- Aciers structurels
- Alliages d'aluminium et de magnésium pour corroyage
- Aciers de décolletage
- Aciers inoxydables
- Alliages de titane
- Alliages de molybdène
- Alliages de Nickel et de cobalt
La plupart des alliages d’acier sont presque toujours forgés à chaud, car à mesure que se produit l’écrouissage sur ces matériaux, leur déformation devient de plus en plus difficile. De plus, il est bien plus intéressant financièrement de forger à chaud des matériaux tels que l’acier, et ensuite d’y appliquer un traitement thermique.
Le forgeage à chaud constitue l’un des meilleurs procédés de fabrication pour produire des formes complexes, des composants lourds ou des alliages très résistants.
Quelles industries peuvent tirer le plus de bénéfices de la forge à chaud ?
Les produits forgés à chaud sont principalement utilisés par l’industrie automobile, le secteur agricole, l’aérospatial et la construction, car ces secteurs sont à la recherche de solidité et de durabilité.
Résumé des avantages de la forge à chaud :
- Bonne ductilité
- Possibilité de créer des pièces sur-mesure
- Excellente qualité des surfaces, bien qu’un usinage des parties fonctionnelles soit généralement requis
- Bonne formabilité
- Contraintes de forgeage réduites, donc moins d’énergie nécessaire
- Diffusion plus importante, et donc manque d’homogénéité chimique réduite.
Setforge, filiale de Farinia Group spécialisée dans la forge, propose toutes les techniques de forge ainsi q’un développement complet des composants forgés à chaud, à mi-chaud ou à froid. L’équipe R&D de Farinia Group, Setforge Engineering, possède une solide connaissance de la métallurgie afin d’ajuster tous les paramètre requis afin de garantir aux clients une conception, une simulation et une exécution parfaite de l’intégralité du procédé.