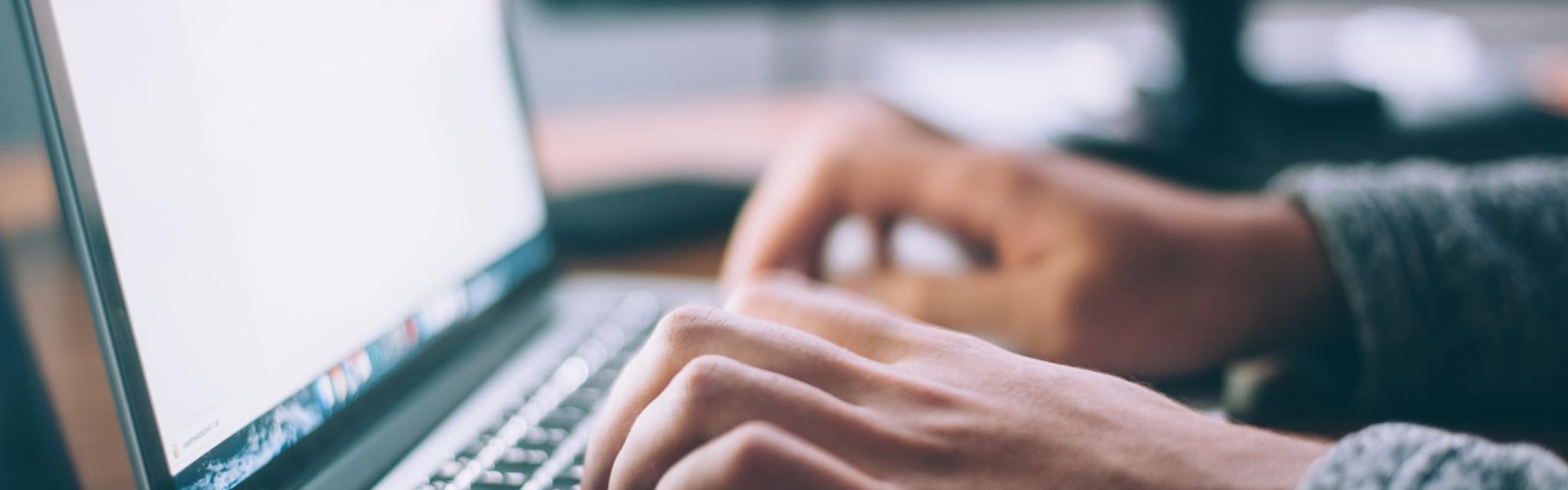
Les techniques de fabrication additive sur lit de poudre offrent aux concepteurs une liberté géométrique incomparable. Il s’agit d’un des avantages majeurs de l’impression 3D métallique par rapport à la fonderie, qui pour sa part implique plus de restrictions : en effet, certaines formes ne refroidissent pas de façon uniforme, ou requièrent des moules ou autres outillages particuliers. Enfin, le processus de fabrication des pièces est plus compliqué.
La liberté de conception de la fabrication additive métallique permet de consolider les assemblages tout en limitant le nombre de pièces. La consolidation présente divers avantages, allant de la simplification de la gestion des données de conception à l’amélioration générale de la sécurité (en limitant les pannes potentielles aux interfaces entre composants). La consolidation d’assemblages permet notamment d’éliminer les accumulations de tolérance et en offre un niveau de précision acceptable pour la majorité des applications (tolérance moyenne : 50-100 µm).
Certaines entreprises qui ont mené avec succès la transition de la production mécanique vers la fabrication additive métallique confirment les avantages liés à la chaîne d’approvisionnement (ex : réduction des cycles de développement et de production) ainsi que les économies de matériaux. En effet, cette méthode produit peu de déchet de matériaux, et sous certaines conditions, la fabrication additive peut même s’avérer être respectueuse de l’environnement.
Du point de vue « matériau » : Au même titre que l’acier inoxydable, les alliages de titane et les superalliages (nickel, cobalt/chrome), l’aluminium fait désormais partie des matériaux employés en fabrication additive. C’est parce que les alliages d’aluminium sont la pierre angulaire de nombreuses industries du fait de leurs exceptionnelles qualités thermiques, leur résistance mécanique moyenne et leur rapport « résistance par unité de masse ».
Quelles sont les applications haut de gamme pour les alliages d’acier ?
Parmi les autres alliages d’aluminium, l’AlSi10Mg est souvent utilisé en tant que composant dans les sports et l’industrie automobiles, ainsi que dans l’ingénierie. L’AlSi10Mg est relativement résistant et dur. Ce matériau a toujours été privilégié pour le moulage de pièces légères aux parois fines, ou de tout autre composant doté d’une géométrie complexe sujet à des charges élevés. Généralement, cet alliage d’aluminium offre une alternative économique au titane dans le cas de composants légers exposé à une fatigue non critique ainsi qu’à des charges mécaniques.
Le choix de l’AlSi10mg est également pertinent pour les composants soumis à des flux thermiques importants, et dont la performance est liée à la vitesse de refroidissement (pièces pour moteurs de voitures ou de motos de course, par exemple). L’importante diffusivité thermique des alliages d’aluminium est particulièrement adaptée aux pièces des échangeurs thermiques.
La liste non exhaustive des autres applications inclut les boitiers de composants, les éléments de tuyauterie, de nombreuses pièces de moteurs ou moules, et divers outils de production.
En cas de besoin, l’AlSi10Mg peut se montrer assez souple en ce qui concerne le post-traitement (traitements de finitions, tels que le grenaillage et les revêtements), ce qui est un avantage indéniable.
L’AlSi10Mg est un alliage particulièrement adapté à la fonderie qui se trouve également être la seule option pour la fusion laser de l’aluminium
Certains alliages d’aluminium (les séries 6xxx en particulier) sont susceptibles à la fragilisation et à la rupture lorsqu’ils sont mis en forme et soudés. Des fissures peuvent apparaître après solidification à cause des contractions thermiques (criques), ou au-delà de la température de « solidus » à cause du phénomène de retrait (criques de retrait).
Les alliages aluminium-silicium sont essentiellement utilisés dans le domaine de la fonderie du fait de leur excellente fluidité de fusion et de leur retrait relativement faible. En ajoutant quelques pourcentages de silicium à l’aluminium, on améliore ses propriétés de façon significative, ce qui réduit ses probabilités de retrait au cours de la solidification. Un retrait moindre permet de limiter la pression, et ainsi de réduire la probabilité de voir apparaître des fissures au cours de la solidification. De plus, si le produit de la fusion est suffisamment liquide, cela permet de combler les fissures naissantes et de consolider le matériau avant solidification.
On peut supposer que la nature quasi eutectique de l’alliage AlSi10Mg sur le diagramme de phrase aluminium-silicium (ainsi que sa température de fusion, relativement basse, qui avoisine les 570°C) explique pourquoi il est si souvent employé en fonderie. Sans surprise, le AlSi10Mg est aussi l’alliage d’aluminium est le plus utilisé par les techniques de fusion laser.
Sous réserve de maîtriser des compétences essentielles, les procédés de fusion laser permettent de produire des pièces structurelles complexes en AlSi10Mg qui sont dotées d’une densité de presque 100%. Il s’agit ainsi d’obtenir une microstructure dépourvue de défauts, une des exigences fondamentales permettant de garantir des propriétés mécaniques comparables, voire meilleure que celle des pièces moulées.
L’aluminium reste fondamentalement délicat pour la méthode de fusion laser, dans laquelle l’expertise compte encore plus que dans le domaine de la forge
Les avantages de l’aluminium sont indéniables. Toutefois, en comparaison d’autres matériaux, l’importante conductivité thermique de l’aluminium et de ses alliages en fait une gamme de matériaux particulièrement difficiles à fondre et à souder ; et ces problématiques s’appliquent naturellement à la fusion métallique, avec des limitations supplémentaires ! En effet, les poudres d’aluminium sont intrinsèquement légères et dotées d’une faible fluidité lors du revêtement des couches de poudre (recoating, en anglais). Enfin, les poudres d’aluminium réfléchissent beaucoup la lumière, donc dissipent rapidement la chaleur, en comparaison des autres matériaux dédiés à la fabrication additive métallique.
Ainsi, la puissance du laser doit être suffisamment élevée afin de lutter contre le refroidissement par conduction et rayonnement des poudres vers leur ambiance en vue de faire fondre les particules de poudre.
Une source supplémentaire de complication réside dans la sensibilité des alliages d’aluminium aux mécanismes de formation des porosités. Cela s’expliquer par la sensibilité de l’aluminium à l’oxydation et à l’humidité.
1) L’oxydation des particules d’aluminium favorise la porosité à cause de la formation d’une mince couche d’oxyde qui se forme rapidement lorsque l’aluminium est exposé à l’air.
De nombreux défauts inhérents à la fabrication de pièces par fusion laser d’aluminium sont identiques à ceux de fonderie traditionnelle. L’oxydation est un phénomène de surface, c’est la raison pour laquelle elle est particulièrement importante en fabrication additive métallique, car la poudre qui sert de matière première offre un rapport « surface par unité de volume » beaucoup plus important.
Les effets négatifs du phénomène d’oxydation dans la technique de fusion laser sont les suivants :
- L’oxydation sur la surface des particules fait obstacle au phénomène métallurgique de « diffusion », et cela limite le frittage entre les particules non fondues. Ce phénomène est responsable de zones de fragilités dans les composants ;
- Les films d’oxydation adhèrent fortement et se former dès les concentrations en oxygène relativement peu élevées ;
- Lorsqu’ils sont piégés dans le bain de métal en fusion, le film d’oxyde est susceptible de capturer du gaz responsable des porosités dans le matériau ;
- La formation de films d’oxydation sur les surfaces métalliques solides et liquides laisse les films d’oxyde entre les passages du rayon laser et à chaque nouvelle couche de la pièce en aluminium ; quand deux films rentrent en contact, cela créé des porosités.
A condition que la poudre soit « toujours » correctement conditionnée et est donc dépourvue de traces d’oxydation, ces effets indésirables peuvent être atténués durant le procédé de fabrication additive métallique en utilisant une atmosphère gazeuse inerte.
Cela étant, il est impossible d’éviter totalement le phénomène d’oxydation, et le procédé de fabrication additive métallique doit détruire cette oxydation si l’on souhaite obtenir des pièces denses à 100%. Ainsi, il est recommandé d’avoir recours à une importante puissance de laser pour travailler les alliages d’aluminium, non seulement pour compenser la diffusion thermique, mais également pour éviter la formation de couches d’oxyde.
2) L’absorption d’humidité est aussi responsable de la formation de porosités. L’aluminium en fusion offre une relativement bonne solubilité permettant à l’hydrogène de demeurer dissous dans le métal en fusion. Cela étant, la solubilité de l’hydrogène est bien moindre dans le métal solide, et celui-ci tend à dégazer derrière le front de solidification.
En conséquence, la porosité de l’hydrogène est plus importante si la poudre contient de la vapeur d’eau ou n’importe quelles substances chargées en hydrogène (graisses, huiles), car ceux-ci se décomposent sous l’effet de la chaleur, et libère leur hydrogène dans la zone de fusion.
Qu’en est-il des propriétés mécaniques des pièces en AlSi10Mg fabriquées par fusion laser ?
En adoptant les précautions adéquates, les pièces en AlSi10Mg qui sont issues des procédés de fabrication additive métallique « sur lit de poudre » possèdent des propriétés mécaniques plus ou moins comparables à celles des pièces moulées.
Généralement mais pas systématiquement :
La dureté Vickers des pièces « brutes de fabrication additive » (ou dites « as-built », ce qui signifie sans traitement de la matière) est significativement plus élevée que la dureté des pièces moulées par injection sous pression dans les conditions brutes de coulée, et presque autant que les pièces moulées par injection sous pression, après vieillissement structurel.
La résistance limite à la rupture des pièces en aluminium « brutes de fabrication additive » est toujours plus élevée que les pièces moulées par injection sous pression dans les conditions brutes de coulée ou après traitement de vieillissement.
La fabrication additive permet d’obtenir des microstructures particulières dotées de propriétés mécaniques uniques parmi lesquelles l’anisotropie (qui est généralement non souhaitée).
Les pièces moulées en AlSi10Mg présentent une solidité et une dureté plus importante au cours du traitement thermique en raison de la précipitation de composés intermétalliques (Mg2Si) ; cependant, la fabrication additive produit des pièces plus résistantes et dures, et ce, dans leur état « brut de fabrication », car le refroidissement plus rapide permet une finesse de microstructure supérieure.
Une autre contribution provient d’une distribution avantageuse du silicium dans la matrice d’aluminium ainsi que de la présence de composés intermétalliques (Mg2Si).
À première vue, on pourrait penser que la fabrication additive à partir d’aluminium est un procédé facile : choix d’une conception, lancement de la machine, et quelques heures plus tard, des composants métalliques exempts de défauts apparaissent dans la chambre… Dans la pratique, la fabrication additive métallique peut créer des défauts, parmi lesquels des porosités, qui altèrent les propriétés, et donc la fiabilité des pièces.
C’est un risque éventuel, et la combinaison de paramètres et conditions non-maitrisées peut être à l’origine de résultats inattendus.
En conclusion, la fusion laser de pièces en AlSi10Mg permet d’obtenir des composants solides, voire de qualité irréprochable, mais cela implique une vraie expertise car les obstacles subsistent tout au long des différentes étapes de production. Cependant, les multiples avantages de l’aluminium en valent largement la peine.
Spartacus3D est engagé dans l’application de la fabrication additive métallique aux composants produits en série. Avec pour valeurs phares qualité et consistance, Spartacus3D concilie les meilleures pratiques industrielles et ressources nécessaires à la fabrication additive de composants en aluminium de haute gamme.