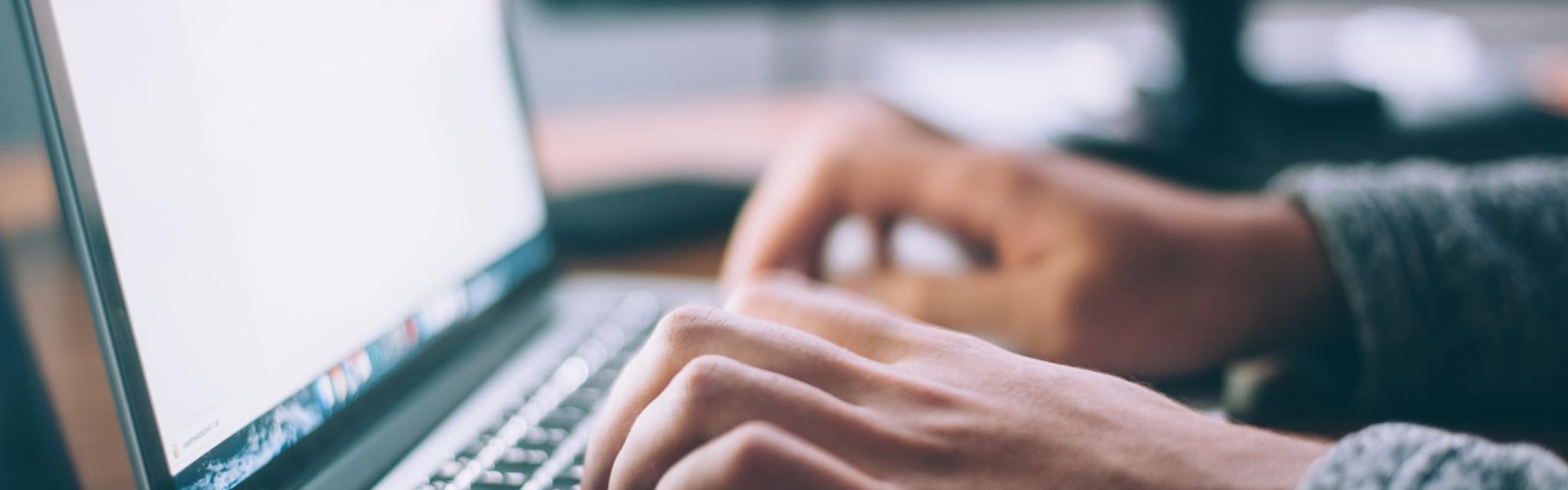
Le secteur de la fabrication additive est un secteur dynamique dont la croissance est intrinsèquement liée aux matériaux disponibles et à leur coût. Et il n’est pas chose aisée de s’y retrouver entre les différentes désignations de procédés de FA et les matériaux utilisés.
D’un côté, le nombre de matériaux métalliques disponibles pour les systèmes de fabrication additive ne cesse de croître. De l’autre, les efforts continus entrepris en faveur de la standardisation des matériaux et des procédés accélèrent la pénétration de la technique dans divers secteurs industriels et l’innovation au sein des chaines de valeurs existantes.
Une grande variété de matériaux disponibles offre un large éventail de possibilités, mais apporte de la confusion quant au choix idéal, s’il existe. En effet, le choix du matériau le plus adapté permet de réaliser un ensemble de spécifications données, qu’il s’agisse de prototypes, pièces uniques, de pièces produites en petite série, ou personnalisés ou de pièces détachées.
Quels matériaux pour l’impression additive ?
Le processus de sélection des matériaux nécessite un compromis qui inclut un certain nombre de facteurs à prendre en compte et à comparer. Parmi ces éléments, on peut par exemple citer l’application, la fonction, la stabilité, la durabilité, l’esthétique, le budget et les priorités du concepteur.
Spartacus3D, en sa qualité de producteur de composants à haute valeur ajoutée issus de la fabrication additive, excelle dans la transformation de certains des matériaux présentés ci-après. Vous souhaitez savoir directement si notre gamme de matières peut correspondre à votre application ? Il suffit de nous contacter.
Voici une liste non-exhaustive des différents matériaux disponibles pour la fabrication additive métallique :
1) Acier à outils et acier « maraging »
L’acier à outils se définit par un ensemble d’aciers au carbone et d’alliages d’acier possédant excellente solidité, résistance à l’abrasion et à la déformation, une bonne tenue mécanique sous des températures élevées.
H13 (1.2344)
Le H13 est un acier à outils pour le travail à chaud, souvent utilisé dans les matrices car capable d’en supporter les conditions extrêmes pour une période de temps indéfinie.
Maraging 300 (1.2709)
Les aciers dits « maraging » (mot-valise de « martensitic aging », c'est-à-dire maturation de la martensite) sont des alliages connus pour leur importante résistance et dureté, tout en gardant une bonne ductilité.
Ces aciers se distinguent notamment par le fait que leur résistance n'est pas due uniquement à leur teneur en carbone, mais est liée à la présence de précipités inter-granulaires.
Grâce à son excellente dureté à et sa résistance contre la fatigue, le Maraging 300 peut être utilisé dans de nombreuses applications pour outils (moulage par injection, moulage d’alliages métalliques légers, poinçonnage et extrusion) ; ce matériau convient également parfaitement à la fabrication de diverses pièces industrielles et d’ingénierie à haute performance (aéronautique et spatial, pièce de cellule d’avion ultra résistantes et applications automobiles).
2) Aciers inoxydables
L'acier inoxydable est un alliage d'acier (comportant moins de 1,2 % de carbone) avec plus de 10,5 % de chrome, dont la propriété est d'être peu sensible à la corrosion et de ne pas se dégrader en rouille.
La présence de chrome en solution au-delà de 10,5 % dans la matrice d'un acier provoque la formation d'une couche protectrice d'oxyde de chrome qui lui confère son inoxydabilité. D'autres composants peuvent être ajoutés, notamment le nickel qui améliore les propriétés mécaniques en général et la ductilité en particulier, ou encore le molybdène ou le titane qui améliorent la stabilité de l'alliage pour des températures autres qu'ambiante, ou encore des éléments à hauts points de fusion comme le vanadium et le tungstène accompagné en général d'une augmentation de la teneur en chrome, pour obtenir la résistance aux hautes températures au contact d'une flamme (aciers réfractaires).
L'acier inoxydable est devenu indispensable dans de nombreux domaines : ustensiles de cuisine, objets usuels, médecine, chirurgie, bâtiment et travaux publics, construction navale, automobile, aéronautique, outillage, industries mécaniques, agroalimentaires, chimiques, transports, etc.
316L (1.4404)
L’acier inoxydable austénitique est caractérisé par sa haute rigidité et sa forte résistance face à la corrosion. Le 316L peut être utilisé sur un très large spectre de températures, températures cryogéniques incluses. Celui-ci peut être utilisé pour diverses applications d’ingénierie, dans l’aéronautique et spatial, le pétrole et le gaz, mais aussi dans l’alimentaire et le médical.
Distributeur fait en SS 316L par une machine EOS M280
15-5PH (1.4540)
L’acier inoxydable martensitique (durcissement par précipitation) est très résistant, résiste extrêmement bien à la corrosion et ne contient aucune ferrite. Le 15-5PH est très utilisé dans les industries aéronautiques et spatiales, pétrochimique, chimique, alimentaire et dans la métallurgie en général.
17-4PH (1.4542)
Cet autre acier inoxydable martensitique présente une excellente résistance à la corrosion, une très bonne solidité et dureté dans des conditions pouvant atteindre 315°C. Il offre également une excellente ductilité lorsqu’issu des procédés de FAM via la fusion laser. Ce type d’acier peut également développer une large gamme de propriétés après traitement thermique.
Tous les aciers au carbone, aciers doux, aciers faiblement alliés et aciers à outils sont ferromagnétiques. Les différentes nuances d’acier inoxydable sont également magnétiques (à l’exception de la nuance austénitique, telle que le 316L), notamment les nuances « ferritiques », « duplex » (mélange d’austénite et de ferrite), nuances « martensitiques » et les nuances durcies par précipitation (15-5PH and 17-4PH).
3) Titane et alliages de Titane CP (commercialement purs)
Grades 1 et grade 2
Les grades 1 et 2 sont disponibles sous la forme de poudre. Le grade 2 est plus solide que le 1 et est tout aussi résistant. Le TI-CP grade 2 offre de nombreuses applications dans l’industrie médicale du fait de son excellente biocompatibilité, en particulier en cas de contact direct avec un tissu ou un os.
Alliage de titane Ti6Al4V (Grade 5)
Le Ti6Al4V est à l’alliage de base de Titane dans l’industrie. Son excellente solidité et dureté, sa résistance à la corrosion, son poids spécifiquement faible en font un matériau idéal pour un grand nombre d’applications d’ingénierie de haute gamme. Il est donc utilisé dans les secteurs de l’aéronautique, du spatial et de l’automobile.
Alliage de titane Ti 6AL-4V ELI (Grade 23)
Le Ti 6AL-4V ELI ou Grade 23 est une nuance de Ti6Al4V possédant une pureté supérieure. C’est l’alliage de titane le mieux adapté aux applications médicales, tels que la dentisterie et implantologie requérant une biocompatibilité à toute épreuve. Ces applications tirent aussi avantage de l’excellente résistance mécanique et à la fatigue et du faible module d’élasticité du Ti6Al4V.
4) Alliage d’aluminium
Les poudre d’alliage d’aluminium présentent un certain intérêt pour les procédés de fusion laser du fait de leurs diagrammes d’équilibre. En effet, la différence entre les températures de « liquidus » (fusion) et de « solidus » (solidification) est très faible, en comparaison de celle des alliages d’aluminium corroyés de haute résistance.
AlSi12 (3.3581)
Il s’agit d’une poudre métallique destinée à la fabrication additive de pièces alliant légèreté et bonnes propriétés thermiques. Parmi les applications les plus communes, on peut citer celles mettant en jeu des parois fines, tels que les échangeurs thermiques, des prototypes industriels, ou des pièces de séries ou de rechanges à destination des secteurs de l’automobile, de l’aéronautique et du spatial.
AlSi10Mg (3.2381)
L’addition de Silicium et de Magnésium permet d’augmenter de façon significative la résistance mécanique du matériau. Cet alliage d’aluminium est utile pour les pièces ayant des parois fines, des formes complexes et est idéal pour les applications nécessitant légèreté et bonnes propriétés thermiques. Enfin, il est possible de traiter thermiquement l’aluminium AlSi10Mg pour en améliorer les propriétés mécaniques. Les pièces en AlSi10Mg issues des procédés de fabrication additive via fusion laser atteignent une densité proche de 100% et possèdent des propriétés similaires aux pièces moulées ou corroyées.
5) Alliages à base de nickel
Les superalliages sont généralement caractérisés par une excellente combinaison de propriétés mécaniques :
- Résistance mécanique en traction et au fluage,
- Résistance à la fatigue thermique et fatigue par corrosion.
Inconel 625 (2.4856)
Ce matériau peut supporter d’intenses contraintes mécaniques à court terme, et ce, à des températures pouvant atteindre près de 815°C. Cependant, il est généralement moins solide que les autres alliages renforcés par précipitation de solutions solides. Pour des garantir une haute résistance mécanique sur le long terme, il est recommandé de ne pas dépasser 595°C avec cet alliage. De plus, il peut résister à la corrosion par solutions aqueuses et chlorure ioniques jusqu’à 980°C, bien que pas moins efficace que le Hastelloy X. Cet alliage est largement utilisé dans les applications à basse température des industries chimiques, notamment les composants soumis à l’eau de mer et ceux des épurateurs des fumées de centrales électriques qui nécessitent une excellente résistance à la corrosion caverneuse ou par piqûres, et pour les fortes températures dans les domaines de l’aéronautique et spatial, des procédés chimiques et de l’énergie.
Inconel 713 (2.4670)
Ce matériau offre une incroyable résistance à la fatigue thermique, ainsi qu’à la rupture à jusqu’à 927°C. Il est par exemple particulièrement adapté aux aubes des étages de turbine de moteurs à réaction d’avions.
Inconel 718 (2.4668)
Il s’agit d’un superalliage à base de fer et nickel, durcissable et doté d’une excellente résistance à la corrosion. Ce matériau, thermorésistant, possède une bonne résistance à la traction, à la fatigue, au fluage et à la rupture à des températures pouvant atteindre jusqu’à 650-700°C. Il convient également très bien aux applications cryogéniques.
L’Inconel 718 convient à une multitude d’applications haut de gamme, parmi lesquelles les composants des réacteurs d’aviation et des applications de production d’énergie terrestre (turbines, anneaux, boitiers, attaches et pièces d’instrumentation).
Rotor de turbocompresseur réalisé en Inconel 718 avec une machine M280
Inconel 738
Ce matériau possède une excellente résistante à la rupture en fluage à haute température, et une excellente résistance à chaud face à la corrosion, bien meilleure que celle de nombreux superalliages haut de gamme à plus faible teneur en chrome.
L’Inconel 738 offre une bonne résistance au fluage. Il est notamment utilisé par l’industrie des turbines à gaz pour des températures pouvant atteindre 920-980°C ; il est également capable de supporter les expositions prolongées à des environnements corrosifs chauds propres aux propulsions d’aéronefs.
Hastelloy X (2.4665)
Ce type d’alliage est caractérisé par une bonne solidité et résistance à l’oxydation malgré des températures élevées, parfois jusqu’à 1200 °C. Il offre également une grande ductilité, même au cours d’une exposition prolongée à des températures jusqu’à 870°C.
Les applications courantes sont dans l’aéronautique et le spatial, ou turbines à gaz terrestres, en particulier pour les composants situés au sein de la zone de combustion, tels que les conduits de transition, parois de la chambre de combustion ou postcombustion, rampes de pulvérisation, portes-flammes, échappement, ou encore en tant que composants de chauffe.
L’Hastelloy X est également résistant à la fissuration lorsque corrosion et tension sont à l’œuvre et peut être utilisé dans les fours industriels, les applications de la pétrochimie et des procédés chimiques (support de catalyseur, four à moufles, chicanes de four et tubes pour la pyrolyse).
6) Alliages de cobalt et de chrome
Ce type de superalliage présente une très bonne solidité et une résistance supérieure à la corrosion; de plus, ces métaux sont non-magnétiques et biocompatibles.
Co28Cr6Mo (2.4723)
Il s’agit d’un alliage généralement utilisé pour les implants chirurgicaux (notamment les articulations telles que les genoux et les articulation coxo-fémorales) grâce à sa très bonne résistance à l’usure, à sa biocompatibilité et sa très faible teneur en nickel (< 0.1%).
Il est également utilisé pour les composants de moteurs, pour les éoliennes, pour de nombreux autres composants industriels, ou encore dans le domaine du luxe et de l’horlogerie.
7) Les alliages de cuivre
Le fabrication additive par fusion laser de composant en cuivre représente un réel défi. Non seulement la conductivité thermique élevée du cuivre évacue rapidement la chaleur du bassin de fusion, mais l’indice de réflexion élevée de la surface des particules de poudre réfléchi une grande quantité d’énergie vers les alentours. En conséquence, un laser de grande puissance est nécessaire et il est parfois préférable d’allier le cuivre à d’autres métaux pour limiter ces difficultés.
CuSn10 (2.1050)
Communément appelé bronze, cet alliage possède d’excellentes propriétés thermiques et électriques.
C’est une solution intéressante pour les applications thermiques, car l’excellente conductivité thermique du bronze peut être combinée à la liberté de conception de la fabrication additive.
Le CuSn10 est souvent préféré pour la fabrication additive de pièces en cuivre, tels que les échangeurs de chaleur. Il est possible d’obtenir des parois fines et des structures internes complexes donnant naissance à des circuits de refroidissement optimisés.
Cela sert par exemple à extraire la chaleur plus efficacement des inserts dans les moules, ou de n’importe quel point chaud.
Spartacus3D s’engage à satisfaire pleinement ses clients, en mettant l’emphase sur l’application finale de ses produits. Notre expertise des matériaux et des machines de fusion sélective par laser (DMLS) nous assure de vous offrir la meilleure solution technique à vos défis de fabrication.