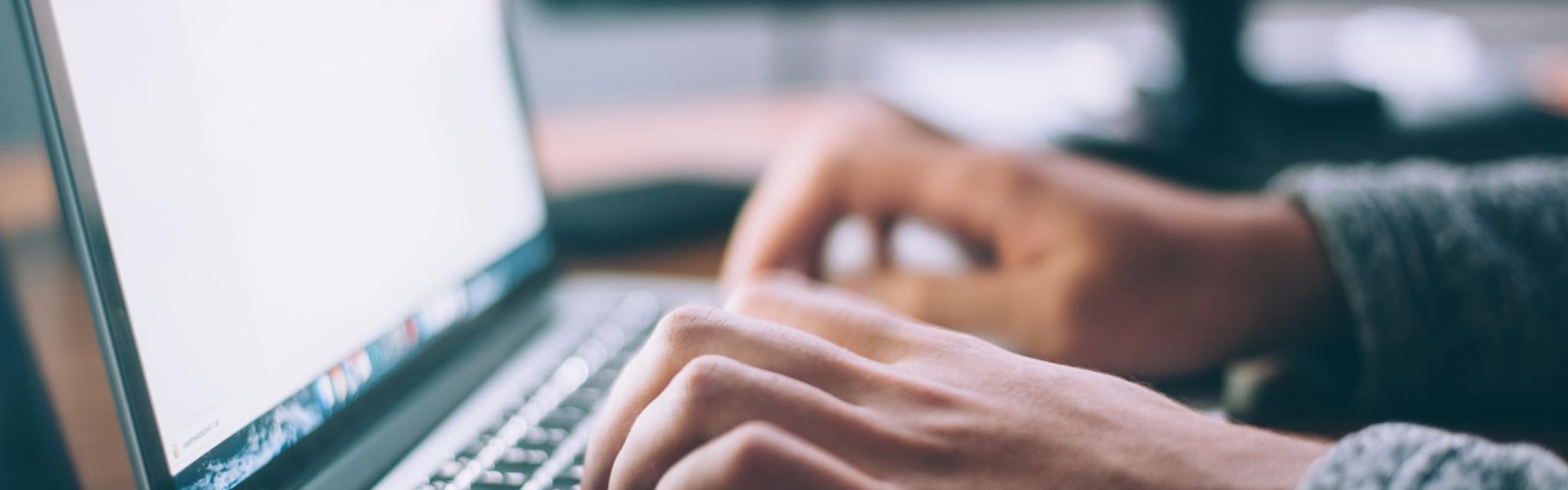
The additive manufacturing market is dynamic and its growth is tied to the available materials and their cost. Navigating through proprietary and generic designations of processes and materials is not an easy task.
Even though the number of existing materials for metal AM system is already impressive, their variety doesn’t stop to expand. Ongoing efforts in materials (and processes) standardization represent an important step for a better comparison between products and a faster penetration into existing supply chains.
The wide variety of materials opens an array of possibilities. Choosing the right material will allow the targeted specifications are achieved, may it be for functional metal prototypes, small series products, individualized products or spare parts.
What metals are available for additive manufacturing?
Material selection process is a trade-off in which a set of factors are considered, compared, weighted and opposed to materials characteristics. The application, function, stability, durability, aesthetics, economics and designer’s priorities are some examples of what can be considered.
Spartacus3D, as a service provider in metal additive manufacturing excels in processing some of the available AM materials presented below. Contact us to know if our materials' offer matches your application.
A non-exhaustive classification of the metals that can be processed through AM can be drawn as follows:
1) Tool steels and maraging steels
Tool steel refers to a variety of carbon and alloy steels particularly well-suited to be transformed into tools. Their suitability comes from their excellent hardness, resistances to abrasion and deformation and their ability to hold a cutting edge at elevated temperatures.
H13 (1.2344)
H13 is a hot work tool steel often used for dies, able to withstand the process conditions for an undetermined period of time.
Maraging 300 (1.2709)
“Martensitic-aging” steels are known for combining high strength, toughness and dimensional stability during aging. They differ from other steels as they are hardened by a metallurgical reaction which does not involve carbon but the precipitation of intermetallic compounds, rich in nickel, cobalt and molybdenum.
Due to the high hardenability and wear resistance, Maraging 300 is suitable for many tooling applications (injection molding, die casting of light metal alloys, punching and extrusion) but also for various high performance industrial and engineering parts (aerospace, high strength airframe parts and motor racing applications).
2) Stainless steels
Stainless steel differs from carbon steel by the amount of chromium present. They are steel alloys with a minimum of 10.5% chromium content by mass. Stainless steel does not readily corrode, rust or stain with water as ordinary steel does.
316L (1.4404)
Austenitic stainless steel characterized by a high strength and corrosion resistance. 316L can be used over a wide temperature range down to cryogenic temperatures. It serves in a variety of engineering applications such as aerospace and oil & gas but also in food processing and medical.
15-5PH (1.4540)
A maraging (precipitation-hardening) stainless steel with a high strength and further hardenable. It has a good toughness, corrosion resistance and is ferrite-free. 15-5PH is widely used in the aerospace, petrochemical, chemical, food processing, paper and general metalworking industries.
17-4PH (1.4542)
Another maraging stainless steel providing an outstanding combination of good corrosion resistance, high strength and good toughness up to 315 °C, with an excellent ductility in laser processed state. Heat treated at a variety of duration-temperatures, 17-4 PH can develop a wide range of properties.
All common carbon or mild steel, low alloy steels, and tool steels are ferromagnetic. Stainless steel grades (with the exception of the austenitic grades, such as 316 L) are also magnetic. Indeed, ferritic grades, duplex grades (mixtures of austenite and ferrite), martensitic grades and precipitation hardening grades (15-5PH and 17-4PH) are magnetic.
3) Commercially pure titanium and alloys
Commercially pure (Grade 1 and 2)
Grade 1 and grade 2 are available in powder form. Grade 2 is stronger than Grade 1 and equally corrosion-resistant against most applications. Cp Ti Grade 2 has numerous applications in the medical industry because it has an excellent biocompatibility, especially when a direct contact with tissue or bone is required.
Titanium alloy Ti6Al4V (Grade 5)
Ti6Al4V is the key stone of titanium alloys industry. The excellent strength and toughness, combined with the corrosion resistance, low specific weight and biocompatibility make it ideal for many high-performance engineering applications in aerospace and motor racing, but also for the production of biomedical implants, due to its higher strength, low modulus and fatigue resistance.
Titanium alloy Ti 6AL-4V ELI (Grade 23)
Ti 6AL-4V ELI (“extra-low interstitial”) or Grade 23 is the higher purity grade of Ti6Al4V. Grade 23 is the ultimate dental and medical titanium grade.
4) Aluminium alloys
Powders of aluminium alloys such as AlSi12 and AlSi10Mg are relatively suitable for laser melting due to the small difference between their liquidus (melting) and solidus temperature (solidification point) compared to high-strength wrought aluminium alloys.
AlSi12 (3.3581)
AlSi 12 is a metal powder for additive manufacturing of light-weight parts with good thermal properties. Typical applications are thin-walled parts such as in heat exchangers, or other industrial grade prototypes, production parts or spare parts for automotive, aerospace and aviation.
AlSi10Mg (3.2381)
The silicon/magnesium combination results in a significant increase in the strength and hardness. This aluminium alloy is used for parts with thin walls, complex geometries and is ideal for applications in need of good thermal properties and low weight. AlSi10Mg can also be heat treated to improve the mechanical properties. ALM parts are fully dense, with similar properties to cast or wrought parts.
5) Nickel-based alloys
Super-alloys are generally characterized by having a good combination of high tensile, creep and rupture strength with excellent tensile, fatigue-corrosion and thermal fatigue resistances.
Inconel 625 (2.4856)
It provides excellent load bearing in short-term applications at temperatures up to approximately 815°C. Moreover, it is generally less strong than other solid-solution strengthened alloys. For long-term elevated temperature service, the use of this alloy is restricted to below 595°C. Moreover, the corrosion resistance is good up to 980°C for aqueous and chloride-ion solutions, but generally not as effectively as Hastelloy X.
This alloy is widely used in low-temperature applications of chemical process industry, sea-water and power plant scrubber that require high pitting and crevice corrosion resistance and high temperature aerospace, chemical process and power industry applications.
Inconel 713 (2.4670)
It offers outstanding resistance to thermal fatigue as well as exceptional rupture strength at 927°C and is ideally suited for jet engine gas turbine blades.
Inconel 718 (2.4668)
This is an iron-nickel-based hardenable super-alloy with an outstanding corrosion resistance. It is heat resistant and possesses good tensile, fatigue, creep and rupture strength at temperatures up to 650-700°C but also an excellent potential for cryogenic applications.
Inconel 718 suits for a variety of high-end applications in aircraft turbine engines and land-based turbines (blades, rings, casings, fasteners and instrumentation parts).
Inconel 738
It possesses excellent high temperature creep rupture strength combined with a hot corrosion resistance better than that of many high-strength super-alloys with lower chromium content. Inconel 738 provides the gas turbine industry good creep strength up to 920 -980°C combined with the ability to withstand long-time exposure to the hot corrosive environments occurring in aircraft engines.
Hastelloy X (2.4665)
This type of alloy is characterized by having high-strength and oxidation resistance at elevated temperatures, and is often used up to 1200 °C. It also exhibits a good ductility after prolonged exposure at up to 870°C.
Its applications can be found in aerospace technology, gas turbine parts and combustion zone components such as transition ducts, combustor cans, spray bars, flame holders, afterburners, tailpipes and cabin heaters.
Hastelloy X is also resistant to stress-corrosion cracking. It is applied in industrial furnaces, for petrochemical applications and the in chemical process industry (catalyst support grids, muffles, retorts, furnace baffles and tubing for pyrolysis).
6) Cobalt-chromium alloys
This class of super-alloys presents high strength, superior corrosion resistance, non-magnetic behavior and good biocompatibility.
Co28Cr6Mo (2.4723)
This is an alloy commonly used for surgical implants as artificial joints including knee and hip joints due to high wear-resistance, biocompatibility, and nickel-free (< 0.1% nickel content) composition.
It is also used for engine components, wind turbines and many other industrial components as well as in the fashion industry to make jewelry.
7) Copper-based alloys
Processing pure copper by laser-aided additive manufacturing (LAAM) is challenging by nature. The high thermal conductivity rapidly evacuates heat away from the melt pool while the high optical reflectivity of the powder diverts large amounts of power to the surroundings. As a consequence, higher laser power is required and alloying copper with other metals is a way to mitigate these difficulties.
CuSn10 (2.1050)
Popularly known as a bronze, this alloy has excellent thermal and electrical conduction properties.
It is a fine choice for heat management applications where the excellent heat conductivity of the copper can be combined with the AM design freedom to give rise to complex internal structure and cooling channels. This enables to cool more effectively tool inserts in molds, for example, or more generally, hot spots such as in semiconductor devices.
CuSn10 is the preferred choice for AM parts in this copper alloy can be micro-heat exchangers, with thin walls and complex shapes.
Spartacus3D endeavours to provide the maximum satisfaction to its customers. By putting an emphasis on the final application of their products, Spartacus3D is able to consider their functional specifications in the light of its technical expertise in materials, selective laser melting capabilities and limitations.