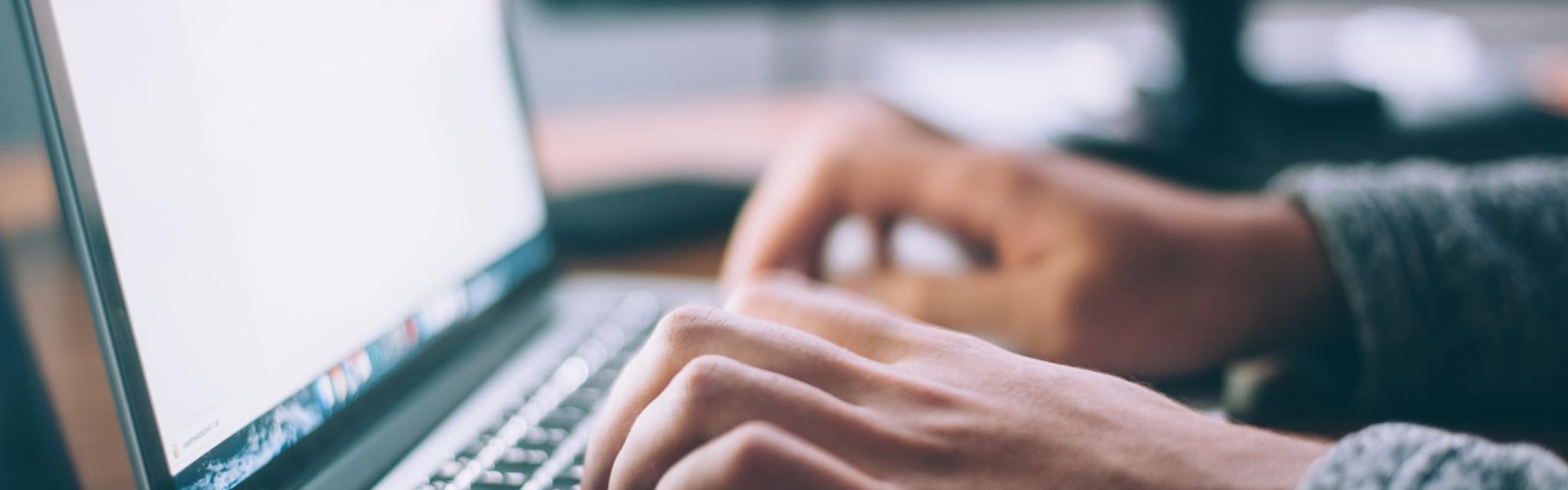
Le procédé de fabrication de forge à froid
Les avantages de la forge à froid
Les inconvénients de la forge à froid
Le procédé de fabrication de forge à chaud
Les avantages de la forge à chaud
Les inconvénients de la forge à chaud
La rentabilité de la forge à froid
La rentabilité de la forge à chaud
Principale différence entre la forge à chaud et la forge à froid
La forge est un procédé de fabrication selon lequel une pièce métallique en phase solide est façonnée par application de forces de pression. Selon la température à laquelle elle est réalisée, le procédé de forge est appelé à « chaud », « mi-chaud » ou « froid ». Les machines utilisées pour compresser et déformer le matériau en pièces à haute résistance peuvent être classées dans les catégories suivantes :
- Machines d’estampage : marteaux de forge, presses à vis, forge axiale et incrémentale
- Presse à mouvement de translation : presses mécaniques et hydrauliques
- Presse à mouvement de rotation : laminoirs longitudinaux et radiaux
- Ensemble de presses avec des mouvements de translation et de rotation : orbite de forge et fluotournage
Structure granulaire des composants forgés
Il est essentiel de noter que le procédé de fabrication de forge diffère de la fonderie qui consiste à faire couler le matériau fondu dans un moule. Cette technique se distingue des autres méthodes de fabrication telles que la fonderie et l'usinage par la capacité de la forge à améliorer les propriétés mécaniques du matériau en affinant sa structure granulaire et offrant le bon angle d’orientation au grain, le rendant plus solide et résistant.
Le procédé de fabrication de forge à froid
Le procédé de fabrication de forge à froid est effectué à température ambiante. La pièce est pressée entre deux matrices jusqu'à ce qu’elle ait pris leur forme. Pour obtenir un composant fini prêt au montage, plusieurs techniques sont utilisées, telles que le roulage, l’étirage, l’emboutissage, l’essorage, l’extrusion et le refoulement en bout. L’extrusion à froid est l’une des techniques de fabrication les plus courantes, et est largement utilisée pour la production de composants automobiles.
Composants forgés à froid
Les avantages de la forge à froid
Certains fabricants préfèrent le procédé de forge à froid à celui de forge à chaud car les pièces forgées à froid ne nécessitent que peu voire aucun travail de finition. En effet, un traitement thermique secondaire avant l'usinage n’est pas nécessaire puisque toutes les barres sont recuites avant d'être forgées. La forge à froid permet de fabriquer des formes proches de leurs dimensions finales, ce qui permet de réaliser une économie de matériaux. Le poids initial de la pièce à travailler est égal au poids final de la pièce forgée à froid, ce qui constitue un autre avantage important. Enfin, les pièces forgées à froid offrent un bon niveau de précision dimensionnelle réalisable et une excellente qualité de surface.
Les avantages économiques associés aux taux de production élevés et à la longue durée de vie de la matrice sont plus que suffisants pour convaincre de nombreux fabricants que la forge à froid est la solution qui leur conviendra le mieux.
Les inconvénients de la forge à froid
Selon les exigences du fabricant, certaines caractéristiques de la forge à froid peuvent se révéler être des inconvénients. Par exemple, à volume élevé, il n’est possible de produire que des formes simples. Les niveaux de déformation réalisables et la qualité de mise en forme sont beaucoup plus limités par rapport à l'estampage. Ainsi, si le client est à la recherche d'un composant spécifique et personnalisé, la forge à froid ne sera pas le meilleur choix pour lui.
Le deuxième inconvénient majeur réside dans le fait que les métaux forgés à froid sont moins ductiles, ce qui les rend inadaptés à certaines configurations. En outre, des contraintes résiduelles peuvent se produire à cause de la structure granulaire du matériau qui lui procure sa force.
Il est important de préciser que l'extrusion à froid exige également un traitement thermique spécifique pour éliminer les éventuelles fissures, la formation de criques ou de chevrons.
Par conséquent, toutes les nuances d'acier ne permettent pas de recourir à la forge à froid, en particulier celles qui ont une faible ductilité ou une sensibilité à l’écrouissage. Par exemple, la forge à froid n’est pas appropriée pour l'acier faiblement allié avec une teneur en carbone supérieure à 0,05%.
Le procédé de fabrication de forge à chaud
Le procédé de fabrication de forge à chaud se fait à une température extrême (jusqu'à 1150°C pour l'acier, de 360 à 520°C pour les alliages d’aluminium, de 700 à 800°C pour les alliages de cuivre). Cette température est nécessaire afin d'éviter l'écrouissage du métal lors de la déformation. L’emboutissage est le procédé de fabrication de forge à chaud le plus répandu : le matériau est compressé dans une presse entre un poinçon et une matrice.
Composants forgés à chaud
Les avantages de la forge à chaud
La température élevée émise pendant lors du procédé de forge à chaud permet d’arriver à un degré extrême de déformation du matériau et d’obtenir des géométries en 3D complexes. Les composants forgés à chaud se prêtent à de nombreuses configurations grâce à leur ductilité accrue. De plus, la technique de la forge à chaud est plus souple que la forge à froid, car elle permet de fabriquer des pièces sur mesure.
L'excellente qualité de surface obtenue permet de mener un large éventail de travaux de finition, comme par exemple le polissage, les revêtements ou la peinture, qui s’adaptent aux besoins spécifiques de chaque client. Les matériaux pour forge à chaud sont disponibles partout dans le monde, ce qui influe positivement sur leur prix final.
Les inconvénients de la forge à chaud
Les propriétés des métaux forgés à chaud sont obtenues par traitement thermique ultérieur, quand le matériau a été trempé à 1 000°C puis à 500°C. Cela nécessite des frais supplémentaires qui peuvent être évités si l'on a recours à la forge à froid - sauf dans les cas de ramollissement, de recuit ou de relâchement.
Autre inconvénient possible : les composants forgés à chaud ont une tolérance dimensionnelle moins précise que les composants forgés à froid. Le processus de refroidissement doit également être effectué dans des conditions particulières pour éviter les risques de déformation. De plus, la structure granulaire de métaux forgés peut varier et il y a toujours un risque de réaction entre l'atmosphère et la pièce à travailler.
Le facteur coût
Ce processus de fabrication complexe peut être affecté par de nombreux facteurs tels que les fournisseurs, les équipements, les styles de gestion, la demande des clients, etc. Plus ces contraintes sont lourdes, plus le risque de perturbation du procédé et de fluctuation du prix final est grand. Cependant, il existe quatre facteurs importants qui déterminent le prix final d'une pièce forgée :
- La quantité de matériau utilisé ;
- Les coûts tels que l'électricité, les investissements, les outils, etc ;
- Les traitements thermiques après façonnage ;
- Les opérations supplémentaires telles que le grenaillage ou les tests de contrôle de qualité.
La rentabilité de la forge à froid
L'optimisation des coûts dans la forge à froid commence dès le choix de la matière première. Celle-ci peut être achetée directement, si nécessaire, avec recuit et écroûtage inclus pour que les lopins puissent être travaillés directement. Les matières premières utilisables pour la forge à froid étant limitées, elles sont, par conséquent, plus coûteuses. Afin de minimiser le coût de fabrication, il est préférable d’avoir recours à la frappe à froid pour les petites pièces.
Pour obtenir le meilleur rapport coût-efficacité, le procédé de fabrication doit être géré par des techniciens qualifiés, maitrisant à la perfection chaque outil ou technique impliqués. Par exemple, les grandes séries de pièces extrudées à froid sont fabriquées sur des presses mécaniques à grande vitesse, mais les pièces complexes en petites séries sont plutôt réalisées sur des presses hydrauliques.
Un système de lubrification efficace joue un rôle essentiel dans l’utilisation optimale de toute pièce forgée à froid. Toutes les pièces doivent recevoir un revêtement en phosphate de zinc ou en polymère. Une lubrification supplémentaire avec de l'huile de forge spéciale est nécessaire sur les presses à plusieurs stations. Un bon système de lubrification garantit la qualité de la pièce finale et élimine les coûts supplémentaires nécessaires pour pallier les éventuels dysfonctionnements pendant le processus.
La rentabilité de la forge à chaud
La minimisation des coûts de l'énergie au cours du procédé de forge à chaud est une préoccupation constante pour tout fabricant. Ceux-ci peuvent être optimisés grâce à l'utilisation d'un inducteur et d'une billette d'un diamètre correspondant, et en installant un système de chauffage flexible à plusieurs étages.
L'automatisation de toutes les presses de forge concernées est essentielle pour l'efficacité des coûts du processus de fabrication de forge à chaud, en particulier pour les industries qui requièrent des cycles de productions élevés, comme l'automobile.
Tous les outils employés doivent être optimisés pour les technologies innovantes suivantes :
- Métallurgie : métallurgie des poudres
- Rechargement
- Traitement thermique
- Traitement de surface : nitruration, cémentation et traitement duplex
Principale différence entre la forge à chaud et la forge à froid
Le procédé de fabrication de forge à froid augmente la résistance du métal grâce à un écrouissage à température ambiante. Au contraire, le processus de fabrication de forge à chaud empêche l’écrouissage des matériaux à haute température, ce qui se traduit par une force de rendement optimale, une dureté réduite et une ductilité élevée.
Le fabricant choisit un procédé plutôt que l'autre pour des raisons économiques et non qualitatives. La décision doit être prise selon l’application du composant souhaité, le type d'industrie et enfin si l’on souhaite produire en masse ou de pièces sur mesure à faible volume.
Setforge fournit des solutions de forge à froid, à mi-chaud et à chaud, ou encore une combinaison de différents procédés pour traiter les demandes diverses de nos clients, réalisées dans d'excellentes conditions et avec des machines de pointe pour des résultats parfaits. Nous travaillons avec nos clients pour comprendre leurs besoins spécifiques et ainsi trouver la meilleure solution possible.