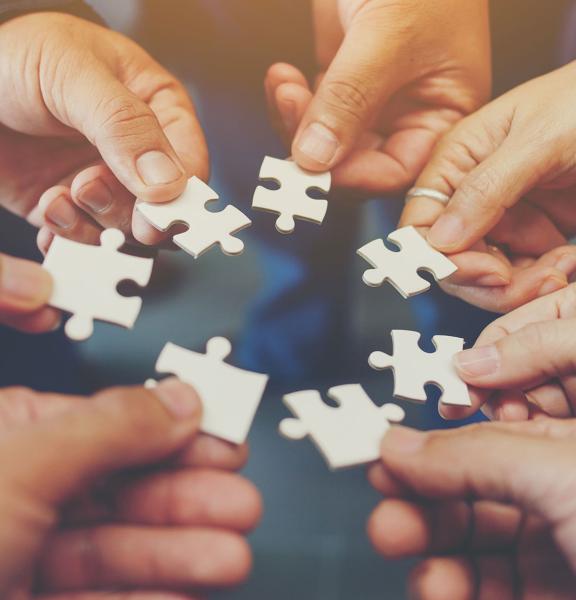
Besides hammers, presses are another compressive force instruments, used in the closed-die forging manufacturing process. The material is “squeezed” between two dies and deformed by the movement of the ram. The main deference between hammers and presses consists in the way how the ram moves. Hammers deform the workpiece through repetitive strokes - from two to several tens, according to the size of the hammer.
The activity of a closed-die forging press ram is typically characterised by:
- one stroke, in some cases 2, to fill the die
- a lower ram velocity:
2 to 50 mm/sec for a hydraulic press
200 to 300 mm/sec for a mechanical press
500 to 600 mm/sec for a screw press: as its velocity is higher, the screw press is an intermediate tool between hammer and conventional presses.
Thanks to the fact that the applied force can be measured and recorded, press forging ensures excellent traceability and repeatability of the production which is more difficult to achieve with drop forging hammers.
The different types of forging presses have different applications:
- Hydraulic presses are used particularly for the manufacture of aluminium components, and heavy steel or titanium components. The biggest press in the world for closed-die forging has a nominal strength of 100 000 metric tons, in France - 65000 metric tons.
- Mechanical presses are used for large series production - usually 10 to 30 000 pieces per month. They are suitable to any material, bur are preferably assigned the manufacture of automotive or truck steel components.
- Screw presses are used for medium series production.
Setforge works with hydraulic, mechanical and screw presses. All of them deliver an excellent degree of mechanical and orientation integrity.
Technical specifications
- aluminumalloys
- carbon steel
- microalloyed steel
- stainless steel
- ni-base alloys
- titanium alloys
- press hot forged components - from 0,1 to 40 kg
- press warm forged components - from 0,2 to 5 kg
- max. length - 550 mm
Companies specifications expand_more
Setforge Gauvin
Setforge Gauvin is specialized in the hot and warm forging on vertical mechanical presses.
Setforge Electroforge
Setforge Electroforge manufactures components with electro-upsetting for a wide variety of industries.
Setforge Estamfor
Setforge Estamfor specializes in hot forging, machinery and assembly. Through our established network of reliable subcontractors, we also supply finished coated parts. Our quality components are highly appreciated by the French and international manufacturing markets.
Setforge L'Horme
Since 1906, Setforge L'Horme, a subsidiary of Setforge, has provided complete manufacturing services including forging, machining, painting, heat treatment and assembly.
Setforge La Clayette
Located in the south of Burgundy, Setforge La Clayette was founded almost 100 years ago, and has a long tradition of metalworking. Our components are made of steel, stainless steel, aluminum, titanium, Inconel and other superalloys.
Setforge Extrusion
Setforge Extrusion is one of the European leaders in the manufacture of cold forged circular shafts or components.
Setforge Barriol & Dallière Industries
Setforge Barriol & Dallière Industries specializes in the manufacture of electro-forged components that can measure up to 5m in length for the automotive industry, heavy goods vehicles and construction machinery.