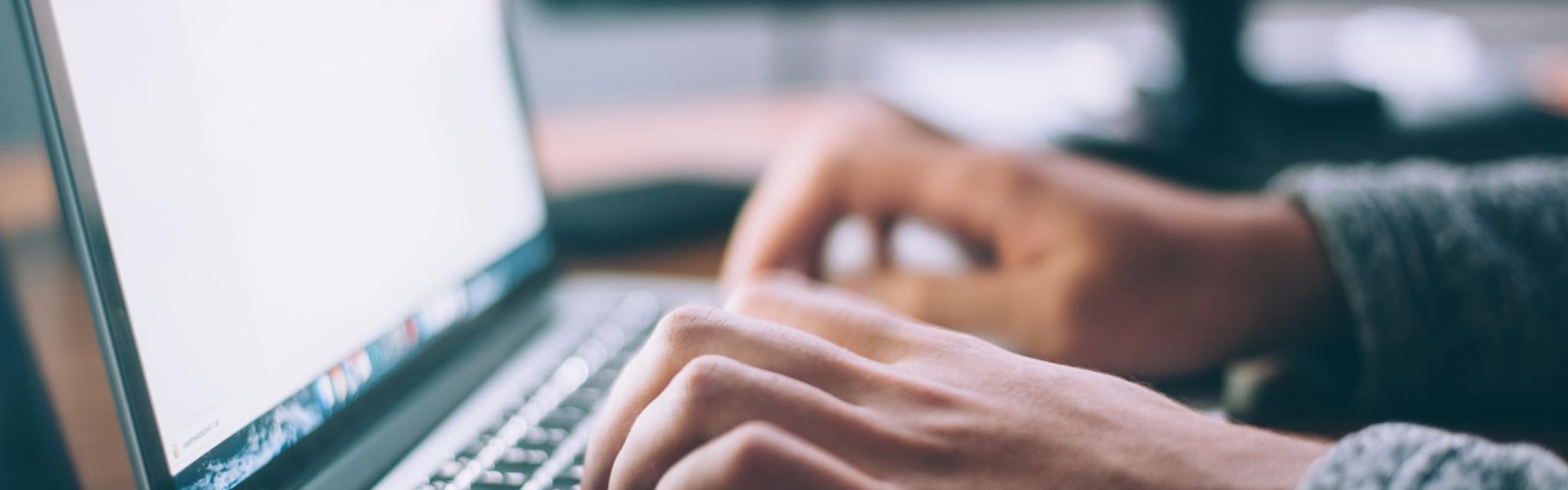
Counterweights are an integral part of a variety of big machines dealing with huge load. By balancing the weight, they secure a safety performance of tractors, forklift trucks, cranes, excavators and others. The manufacturers prefer using either full cast iron, full concrete, or a mix of concrete and metal bits. For example forklift counterweights are commonly made of metals for maximum space utilization. But some industries as agriculture (tractors) or off-highway (excavators and cranes) have counterweight needs that can be fulfilled by both - metal and concrete. Although concrete is cheaper than iron, it's wiser to choose iron, since concrete applications are prone to many problems, that cast iron counterweights can overcome.
Advantages of cast iron counterweights compare to concrete ones:
Density
Cast iron is denser than most materials, thus cast metals for counterweights have in average three times more density than pure concrete. This enables iron to achieve the target weight in less space and volume compared to concrete which eliminates the cost for additional material.
Product Cost
Concrete's density can be improved by adding dense aggregates such as limonite, hematite, or magnetite, or metal bits and scraps into the concrete mix. This increases the concrete's cost substantially, but its density is still less than those of the iron.
Fragility
Cast iron is indeed stronger and harder than concrete which automatically makes counterweights more resistant to impact and strains and guarantees longer fatigue life against cyclic stress. Usually counterweights need screws for fastening or mounting additional equipment. The concrete's surface cracks easily and hardly supports any additional constructions.
Shaping
In usages where counterweights need to fit into specific shapes, for example tractor suitcase counterweights are differently shaped according to space on rear axle of tractors; concrete turns to be more expensive to carve out the desired shape into it. Cracking is less likely to occur, when creating a finer shape on cast iron.
Environmental Impact
Cast iron is a product of recycling and doesn’t require any extraction of new raw materials, which is not the case with concrete.
FMGC strongly recommends the usage of cast iron counterweights over concrete ones. Our foundries are specialized in sand casting of laminar iron. Any kind of additional treatments on the product such as finishing and primer paint coating, belong also to our expertise.
FMGC has high production capacity and is able to support single production or high volume long production runs. Equipped with sophisticated machinery, tooling and experienced manpower, we supply a wide range of counterweights to different industries.