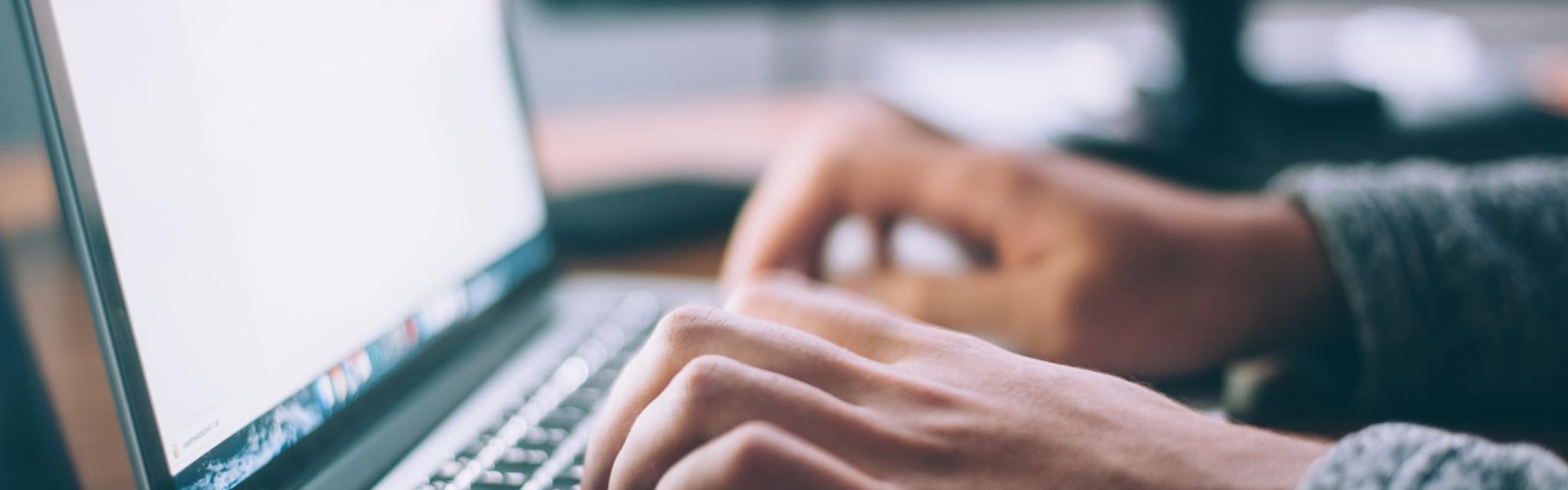
The global medical industry faces challenging problems due to the rising prevalence of unhealthy lifestyles and an ageing population, more at risk for a variety of medical conditions. Undoubtedly, a demand for more medical devices and effective health cares will follow.
Lately, breakthrough advancements in additive layer manufacturing (ALM) were reported in the field of medical technologies. The emergence of digital healthcare and scan-to-part seems now a reality, about to push medical market during upcoming decades, allowing whole new business models and supply chains to flourish.
Patients will benefit further from medical 3D-scanners (computed tomography, magnetic resonance imaging, ultrasound or intra-oral laser), by having their anatomy digitalized to supply blueprints for tailored 3D-printed products. ALM is paving the way for a whole new approach to patient care which provides effective and affordable solutions to more people. Several printed devices already received US FDA clearance, a noteworthy step forward.
What applications for ALM in medical technologies?
- Generic items (hips, knees and spine implants, shoulder anchors, trauma implants such as plates, screws and nails),
- Bespoke patient-specific items (hearing aids, shoe insoles, dental stones, limbs prosthetics for amputees, orthopaedic implants for accident & illness victims such as cranial, jaw, facial bone implants,instruments and surgical guides for medical procedures),
- Patterns for downstream processes (metal casting of dental crowns, plastic vacuum-forming to make dental aligners).
What are the advantages of ALM for the medical industry?
- Shorter manufacturing process for customized items.
- Simplified multi-step production processes.
- Less inventory (lower number of sub-components and demand-based manufacturing).
- Localized distribution of the end product near the customer.
-
Bio-compatibility of metals printed
Medical grade Ti6Al4V titanium alloy is available in ALM powder. It is a widely used alloy in orthopaedic applications because of its excellent tensile and fatigue resistance properties, corrosion resistance along with low specific weight and bio-compatibility. The highly controlled ALM atmosphere (argon, nitrogen, restricted oxygen) preserves these qualities by ensuring high purity parts.
Stainless steel 316L and cobalt chrome alloys are other materials biocompatible and printable by ALM.
-
“One-off” customized metal implants
Traditional manufacturing of bespoke implants is time-consuming and expensive. Fortunately, ALM's flexibility reduces the capital required to achieve scope and facilitates an increase in the variety of products. Therefore, it reduces the costs associated with production customization. Patient-specific products provide a superior comfort and lead to a faster recovery.
Custom shapes optimize the distribution of stresses on bones whereas better adaptation removes the need for certain manual works performed by surgeons in the midst of a procedure. It reduces surgical time, failure risks, and overall costs.
-
Superior mechanical properties:
Powder/laser beam interaction, scan velocity and laser spot size determine the microstructure and melt pool size. Because the temperature gradient is highest around the melt pool, an extremely rapid heat extraction occurs in this so-called “heat affected zone” and very refined grains germ in the microstructure.
ALM presents unique metallurgical aspects and improved mechanical properties are achievable, compared to traditional manufacturing techniques such as casting, for example. Section thickness can be reduced during the design, which permits to lighten parts and decrease patient discomfort, without sacrificing the ability to make complex freeform shapes.
-
Higher complexity designs, in fewer steps:
ALM allows the fabrication of a dense, load-bearing structure that provides strength, combined with a precisely shaped, well interconnected porosity that induce better bone ingrowth into implants and fixation with surrounding tissues. Traditionally, titanium implants are manufactured by subtractive machining where material is removed to create shapes, and then a porous surface coating is added. Last but not least, the raw ALM rough surface (often undesirable elsewhere) also enhances bone-implant fixing.
Such a synergy between the raw ALM part and its function is unusual. Yet not systematic, when a coarse roughness is desired, some downstream operations can be eliminated.
While tailoring surgical implants with greater precision leads to less downside effect and faster physical/psychological recovery, printing them with ALM stands to revolutionize the medical industry in terms of costs and performance.