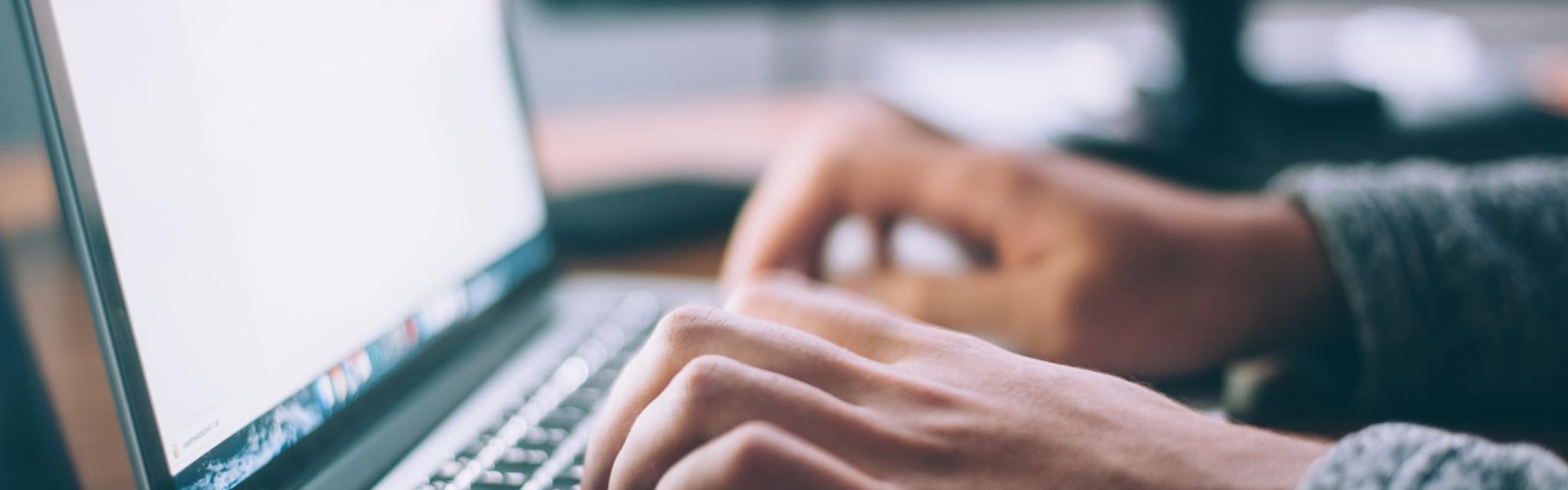
Additive Layer Manufacturing (ALM) prints mechanical parts with an extreme degree of complexity, giving form to supposedly impossible geometries and about every imaginable shape. With ALM, engineers can emphasize on design or functional optimization, rather than machinability.
However, such potential for design refinements strengthens the need for ensuring that metal ALM leads - at least - to similar mechanical properties than traditional manufacturing (casting, forging, milling, etc.).
At Spartacus3D, we are committed to deliver parts with the best mechanical properties. We endeavour to perfectly master Key Process Variables (KPVs) and every metallurgical transformation occurring at each step, from powder melting to post-process operations.
Mechanical properties are dependent upon the microstructural characteristics of the part. In this first section, we will review what elements affect such characteristics during the selective melting. Implications of post-processing operations are discussed in the second part.
Typically, material properties indicated by powder’s suppliers in datasheets are:
- Hardness
- Ultimate tensile strength (Rm)
- Yield strength (Rp2%)
- Elongation at break (A%)
- Young’s modulus (E)
- Fatigue (σd)
Higher density is lower porosity
Even though powder-bed based ALM may be the unique process able to print controlled porosity parts (filter elements, fluid permeable components), most developments (process and powders) have been focused on getting denser materials to maximize material properties and minimize defects generation (including micro-porosity and lack of fusion between neighboring layers).
In order to produce parts with higher density in combination with low surface roughness, one needs to optimize the most influencing parameters for a specific material, which can be divided into four groups:
- Material specific parameters (grain shape, size, distribution, flowability, etc.),
- Laser parameters (laser beam power, spot size, focal point, etc.),
- Scan parameters (scan velocity, hatch distance, etc.),
- Environmental parameters (protective gas atmosphere, ambient temperature, O2 level).
Generally, the densities reachable with ALM are similar or better than those attained with metal injection molding or casting. ALM parts can reveal a density higher than 99.5% and defects usually smaller than 50 µm (<100 µm for IN718). While a residual porosity can’t be avoided in ALM powder bed based processes, it can still be minimized.
It is noteworthy that material’s heterogeneity, thus porosity, has a very detrimental influence on fatigue resistance because of a higher likelihood of crack initiation at pores close to the part surface and subsequent propagation. More moderately, others mechanical properties (yield strength, corrosion resistance, ductility) are also sensible to density.
What is fatigue? Each material has a specific weakening behavior when exposed to repeatedly applied loads, which is called fatigue. In the case of Fe or Ti based alloys, it is possible to determine the fatigue limit below which fatigue failure should never occur.
Powder quality must be considered first…
Powder quality has a significant impact on the ability to produce components that meet stringent specifications consistently. The powder layer density should be as high as possible in order to produce dense parts with high scan velocities and therefore with high productivity. The density of a powder layer is particularly dependent on the particle shapes, sizes or more exactly size distributions.
Particle shape influences porosity because a greater deviation from spherical shape leads to a lower density, thus more porosity. Additionally, spherical shape also offers better flow properties during recoating.
Particle size defines how easily it melts and the final pore size. While a fine powder granulation generally leads to better densities and surface qualities than a coarser material, a particle size distribution has to be qualified against the background of the layer thickness selected.
In all cases, the “effective” (tapped) powder layer thickness should be relatively higher than the diameter of most of the powder particles, allowing most of the particles to be deposited within it.
A sufficient amount of fine particles is also necessary, to fill the voids between the coarser grains. However, should the amount of fine particles (about 5μm or less) be too high, their tendency to form low density agglomerates (owed to electrostatic forces) eliminates their positive effects of filling up voids and thus it becomes difficult to create appropriate, homogeneous powder layers with a high density.
…And "build" parameters thoroughly adjusted…
Although it is possible to get high-density parts from different types of powders, the "build" parameters must be adjusted accordingly, affecting the productivity (speed).
When the laser is scanning the powder layer surface, a certain degree of "re-melting" is inevitable within the last few layers deposed but, correctly adjusted, it can help increase the density by removing aligned porosity or some irregularity.
The extend of "re-melting" depends of the laser power density, the scan speed and the heat evacuation rate of the partly-built part. For a given power and heat extraction, while highest speeds result in insufficient melting, the metal density decreases at lowest speeds due to voids created when the laser enters "keyhole mode" and drills into the layer.
Moreover, a thin powder layer will ensure proper interlayer bonding and a higher density, but it will decrease productivity.
The second part, describes mechanisms affecting mechanical properties during post-processing operations (pre-finished microstructure, anisotropy, stress-relief, age-hardening, shot-peening....)