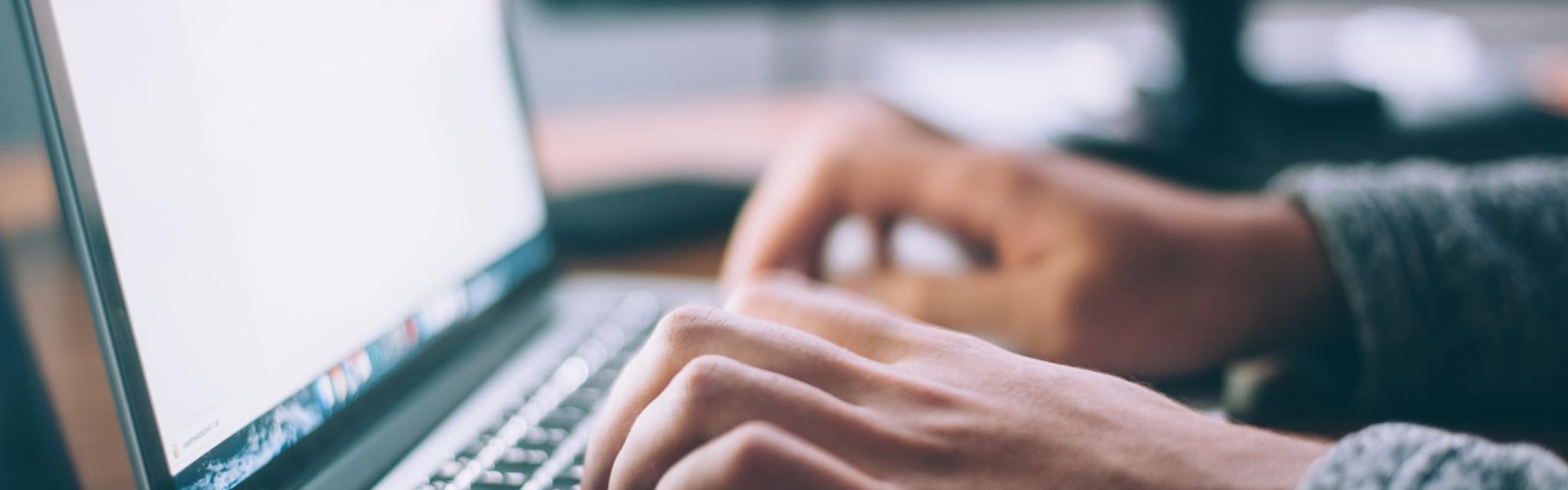
Since its arrival on the consumer market, additive layer manufacturing (ALM), also called “3D-printing”, has become extremely popular since many individuals printed amazing creations. It has sometimes been described as the 3rd industrial revolution.
"Revolution" stands for the drastic changes in the way we do things. The 2nd industrial revolution has seen successive innovations, such as mechanical production of electricity, fossil-powered internal combustion engine, chemical industry, telegraph and telephone, railways and aerial transportations. All of them have enabled significant productivity gains, promoting international trade and impacting human life quality.
The “machine age” is a remarkable period of this era and refers to the early adoption of most traditional manufacturing techniques (milling, drilling, turning, etc…). Usually machining away material in order to achieve a desired shape, they are known as "subtractive manufacturing" methods. Over time, amazing improvements were achieved, . Even though they are still largely dominant within industry today, intrinsic disadvantages of subtractive methods can't be ignored anymore, especially the cost due to material wastes and the machinability restrictions.
Whether disruption or evolution, ALM will induce economic and social far-reaching changes in various business models and it can offer a competitive advantage to the middle market. However, from an industrial standpoint, it would be more than hazardous to affirm that ALM will rid the business world of traditional manufacturing. More of a major evolution than a revolution though.
Manufacturers will change for new production processes only if requirements of cost-effectiveness, improved customers satisfaction and product functionality are met. ALM keeps on paving its way to rapid manufacturing of many “end-user” product applications since recent improvements have strengthened the advantages of additive manufacturing process.
Advantages of ALM over traditional manufacturing processes
-
Reduction of tooling
As tooling is not anymore required, associated costs or lead times to produce them are eliminated, thus shortening time-to-market. Production delays due to damaged or worn tools are also avoided, along with tool maintenance, repair, scrap, and storage.
-
Agile manufacturing
Tool-free manufacturing allows a company to modify a product on a short notice. Such flexibility encourages a higher variability of design, ultimately customization in order to target many customer groups. Helping manufacturers to react faster to changing market conditions by adapting production rates to match orders or adopting “on-demand” manufacturing, ALM translates a production into just-in-time manufacturing.
-
Inventory reduction
With “just-in-time” operations and design consolidation of several sub-components into fewer complex parts, smaller inventory could be held. Onsite storage and warehousing needs could be reduced, freeing up capital to invest in R&D or other business areas.
-
Decentralized manufacturing
As a single printer can build complex parts, large centralized factories with assembly lines are no longer required to achieve economies of scale. Moving all or part of the manufacturing on a regional or even a local basis, closer to the point of sale, becomes economically viable (further reducing shipping time and costs).
-
Design consolidation
A key benefit with ALM is the ability to design products with fewer, but more complex parts, rather than numerous simple ones. This immediately cuts costs and delays caused by documentation, production planning and quality inspection (even if ALM is facing tough challenges in quality control). Less time and labor are required for assembling products. The reduction of the manufacturing footprint (positioning of production and operation activities in terms of value chain and geographical location) may be an additional aftereffect, decreasing the exposure to risks such as changes in local and global demand, currency exchange rates, labor and transportation costs, or even trade regulation.
-
Light-weighting
Producing objects layer-by-layer intrinsically results in parts that satisfy, with less material, the same functional specification. Reducing weight may be as simple as reducing the thickness of a feature in regions of low stress, or as complex as using methods of topological optimization. A third method is “lattice-structuring” design, which retains the external form of the part but employs a lattice or mesh structure of solid material within it.
Just because a part can be produced using ALM doesn’t necessarily means it should be…
Generally, ALM is considered economically suitable for low-volume, complex and small parts. When one tries to determine whether a particular part can be additively manufactured advantageously, one must inspect the entire supply-chain.
It may be relevant to consider a detailed cost/benefit analysis if a part falls into one or more of the following scenarios:
- Expensive to manufacture - because of high design complexity, costly material wastes, high fixed costs (tooling, etc…) or low volumes.
- Long lead times - because it takes too long to get certain parts, downtime costs are too high or there is a need to speed up time-to-market.
- High inventory costs - due to overstock or understock, obsolescence or long-tail (selling a large number of unique items).
- Sole-sourcing suppliers - of critical parts, which causes a supply-chain risk.
- Remotely located operations - where shipping parts is difficult (costly) and time-consuming.
- Substantial import/export costs - because of the location of a business unit or supplier.
- Potential functional gain - beyond what was previously possible, to improve performance.
- Limited product performance/functionality - due to traditional manufacturing limits.
Thanks to its robust market capabilities, additive manufacturing is used already across several industries. Today, aerospace and automotive are the most promising industries for ALM application, while it keeps on spreading as well within the medical sector and several consumer industries (sport, luxury and home appliances).
Looking forward to bringing the best technical solutions to its customer’s challenges, Farinia Group is committed to developing strong capabilities and valuable expertise in metal additive manufacturing through its subsidiary : Spartacus3D.