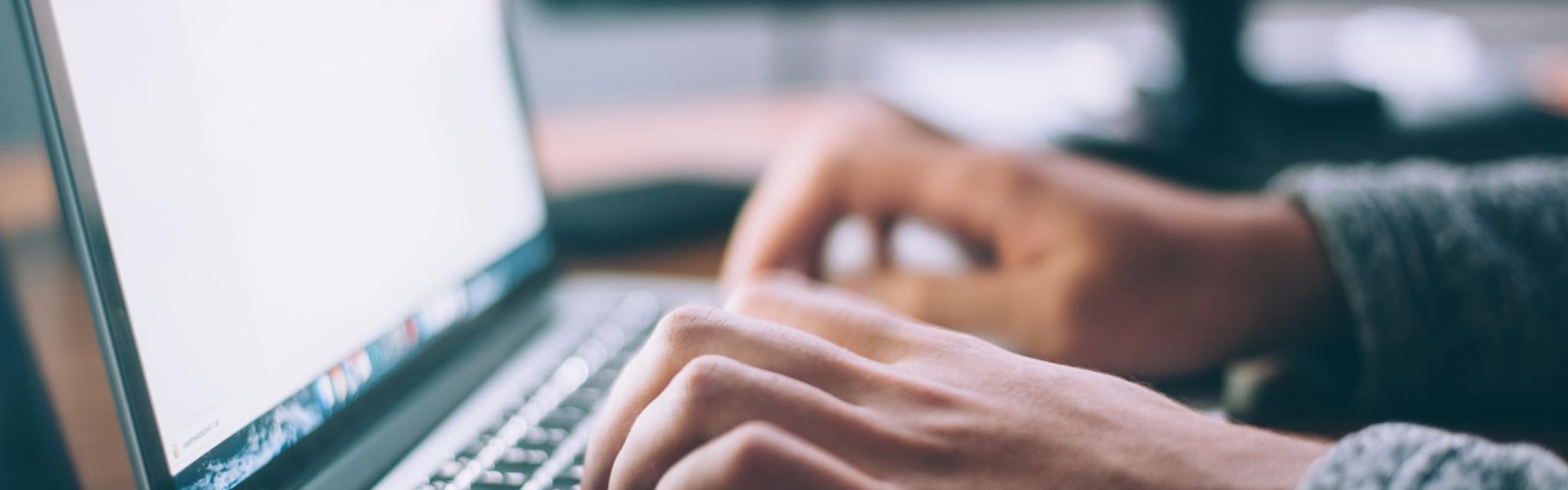
Aerospace industry comprises the national security sector, access to space and any other kind of air transportation. While space travel is still in its infancy and all air military applications are main concern of governments, aviation has become indispensable for ordinary people. Aviation is a solid foundation of a nation’s economic growth providing large numbers of high-value jobs and significant revenues. In today’s global world, connecting people and shipping freight through fast and cost-effective transportation has become essential for international trade and tourism.
As a leader in driving today’s global economy, aerospace has a long history of latest technology inventions’ early adopter and ultimate trendsetter in manufacturing. New materials, state-of-the-art manufacturing processes and sophisticated software were created and absorbed by this industry decades ago and are now common for other industries.
In contrast to mass-production industries, aerospace industry is largely focused towards complex and low-volume production. Besides endless opportunities, globalization also brings unprecedented challenges such as environmental performance restrictions, high manufacturing costs and competitive market conditions.
How Can Aerospace Industry Benefit from ALM?
Aerospace eyes Additive layer manufacturing (ALM) as a way to overcome some of these challenges. ALM has gone a long way from the early stages of its deployment, 30 years ago. The most largely widespread ALM process for industrial applications builds parts layerwise on a powder-bed, selectively melting powder particles by means of a laser or an electron beam.
Generally, ALM challenges the traditional dilemma between scale and scope that prevails in manufacturing in two ways. First, it reduces the capital required to achieve economies of scale. A single printer can simultaneously build several complex parts with variable designs. Therefore, large centralized factories with assembly lines are no longer required (barriers to entry for manufacturing into a location are lowered). Second, it increases the variety of designs that an amount of capital produces. Hence, complexity, production changeovers and customizations are cheaper.
Particularly, ALM technology offers various advantages to aerospace industry:
-
Shorter development process and time to market
ALM allows the rapid prototyping and conceptual design review and validation. Tooling manufacture can be skipped and one can go straight to finished parts. This enables engineers to test multiple configurations, find out customer preferences and minimize product-launch risk.
Advantageous for Aerospace one-off unit (i.e. demonstrators) and low-volume production, ALM reduces or eliminates the cost for expensive and poorly amortized tooling.
Additive manufacturing suits well for collaborative engineering and crowd-sourcing ideas through remote cooperation. It will surely affect how companies manage R&D.
-
Freedom to design complex geometries
ALM gives rise to near-net shape parts and allows increasing design complexity without inflating manufacturing costs. It is doubtlessly the main advantage of the technique for Aerospace given several key repercussions:
-
To maximize performance
Traditionally, designs optimized for topology are seldom producible because of complex shapes. Engineers used to think geometries in respect with the possibilities and limitations of the conventional processes employed (milling, casting, forging, turning, welding, etc…).
In contrast, ALM offers superior flexibility in terms of feasible geometries and creates more space to innovate and explore new design. It allows designers to better serve maximum performance without need to accommodate manufacturing limitations. Complex components can be built up out of a variety of plastics and particularly metals such as steel or aluminium.
Aerospace industry already succeeded to additively manufacture some aerospace components with complex geometries, made of exotic materials such as Titanium Ti6Al4V and Inconel 718, which are traditionally difficult to shape without compromising their excellent (and desired) properties.
-
To consolidate design and improve reliability
The higher design freedom allows decreasing the number of sub-components that compose system assemblies. As a result of fewer components, assembly time and costs are reduced while eventual design modifications are easier.
In theory, consolidating design means joining less or no parts together (by welding or any other method). In ALM, a design can be simplified and consolidated simultaneously, to improve reliability (and durability) of aerospace and aircraft components.
-
To achieve light-weight and improve fuel efficiency
ALM undoubtedly helps reduce weight of aerospace components by printing more efficient geometries, topologically optimized and lattice structures that carve out significant amounts of unnecessary material.
1 kilogram removed from every aircraft of a 600+ fleet of commercial jet-liners saves every year about 90’000 liters of fuel and avoids the emission of 230 tons of CO2 in the atmosphere. It also cuts down on fuel bills, which, in 2013, absorbed 35% of American Airlines’ total operating expenses.
Therefore, weight is a key driver for airlines because lighter aircraft have double impact on the industry. It leads to lower fuel consumption (and CO2 emissions) and to the competitive advantage of reduced costs and better airfares.
Space vehicles require intricately designed parts too, in order to minimize packaging space and weight. Produced in very small volumes, they are expensive and time-consuming when traditionally manufactured.
-
-
On-demand and on-site spares manufacturing
In order to prevent grounded aircrafts, spares have since long been maintained into inventory. While relevant for spares that are low-volume, complex, out-of-production or required at remote locations, it is known that many spares remain unused until they become obsolete.
Removing the need to have tooling inventory already offers a cost advantage for manufacturers, but ALM go farther in reducing warehousing and obsolescence costs by allowing on-demand and on-site manufacturing of spares.
Agile manufacturing is even more effective to cut delays and costs when it is extended to space operations. The required parts, spares and tools can be directly produced in the space station rather than sent within rocket from earth.
-
Higher material efficiency reduces costs for certain components
Some metals are keystones in Aerospace applications, such as the light titanium alloys (mainly Ti6Al4V) or heat-resistant super-alloys (such as Inconel 718). They are hard, expensive and relatively difficult and long to machine. Depending on the geometry, the traditional production may be time-consuming, involve a high wear of cutting tools and large amount of material wastes.
The resulting high “buy-to-fly” ratio leads to recycling operations of costly materials losses. While such materials in their powder form are more expensive, ALM creates far less material waste.
-
In-process quality assurance reduces overall lead time
Aerospace, as an industry obsessed by performance and reliability, has since long performed quality assurance downstream to manufacturing. A critical stage for Aerospace manufacturers in which any serial production often have to meet high specifications to satisfy stringent applications with high quality to ensure reliability. Insomuch that quality assurance can account significantly in the overall lead time and overall cost.
Aerospace industry is the largest source of demand for ALM production-grade systems. While many mechanical testing standards are applicable to parts made by ALM, there is sometimes a real challenge in applying some usual quality control procedures. After-build inspection of complex shapes is more difficult and becomes very challenging or impossible when multiple parts are printed together, assembled and undismantable.
One of the most promising developments in metal ALM production systems concerns the real-time and closed-loop in-process quality control. In powder-bed ALM processes, the material is elaborated in parallel, as the part is shaped.
Monitoring the system settings and process parameters during the ongoing manufacturing permits to regulate and optimize conditions. Mechanical properties in metal additive layer manufacturing are all about metallurgy. In-process quality assurance and control will ensure the repeatability of parts with high material quality and consistent mechanical properties, which is essential for aerospace industry.
In-process inspection of the material health and dimensional accuracy will surely unlock the power of ALM technology for serial aerospace production as qualification and consistency variation are now the main concerns. Moreover, it will ultimately decrease unit costs of ALM components by reducing costs associated with quality control.
Spartacus3D understands in what extend ALM is a natural fit for Aerospace manufacturing, even though it still has space for improvement before it can unleash its full potential for this exacting industry.