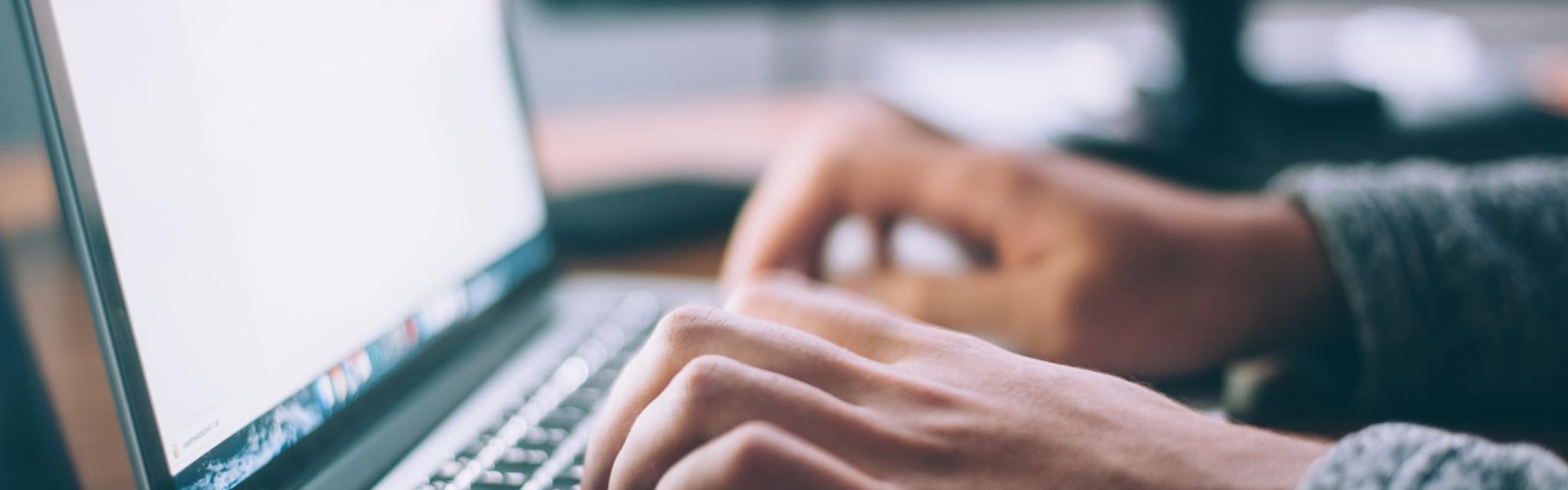
In the common rail fuel injection system, a common rail is designed to deliver pressurized fuel to multiple injectors. This configuration can be prone to failure if its manufacturing quality is not sufficiently monitored. Common rail problems can be caused by many factors and the first one is their design. The next-generation gasoline and diesel engines tend to become smaller and lighter. This has a huge impact on the common rail shape which should conform to the new engine requirements and support high pressure.
How does a common rail product design affect its quality?
Defects in the Heading Manufacturing Process
The heading manufacturing process is a metal forging process, typically used to shape components with a “head” which is larger than the rest. This occurs usually at the end of the bar. In the case of the common rail, the “heads” are the joining points between the pipe and the injectors. A poor design can create defective folding or buckling on those points that are crucial for the entire common rail system. These deformations on the other hand lead to uneven and defective inner surface which initiates cracks through contact with the high-pressure fuel flow. Hot heading is closely related to upset forging or hollow forging. This is another manufacturing process which increases the diameter of the workpiece by compressing its length in huge presses. This tooling requires specific size of the workpiece, which if not determined properly during the design phase, will cause plenty of defects later.
To secure the perfect performance of the common rail, the exact heading and upsetting parameters must be determined prior to the manufacture, in particular during the design process. The parameters should include the right heading angle, exact heading curvature, and pinpoint upsetting length to minimize formation of cracks.
Pressure and Temperature Fluctuations
Pressure and temperature change drastically (dropping below or climbing over the electronic control unit's ECU input conditions) if there is excessive fuel spread in the common rail. This occurs if the component’s design is not proportional to the desired fuel volume and pressure level which eventually impairs thermal efficiency and performance.
To prevent this problem, the exact dimensions of length and section diameter should be determined in the very first stage of the design in order to make it possible for the common rail to handle the desired pressure and volume level later.
The Setforge manufacturing process starts with our design expertise, corresponding to client’s requirements. A team of professionals is always ready to assist you with know-how and unlimited engineering capabilities in planning your common rail design and manufacturing process.