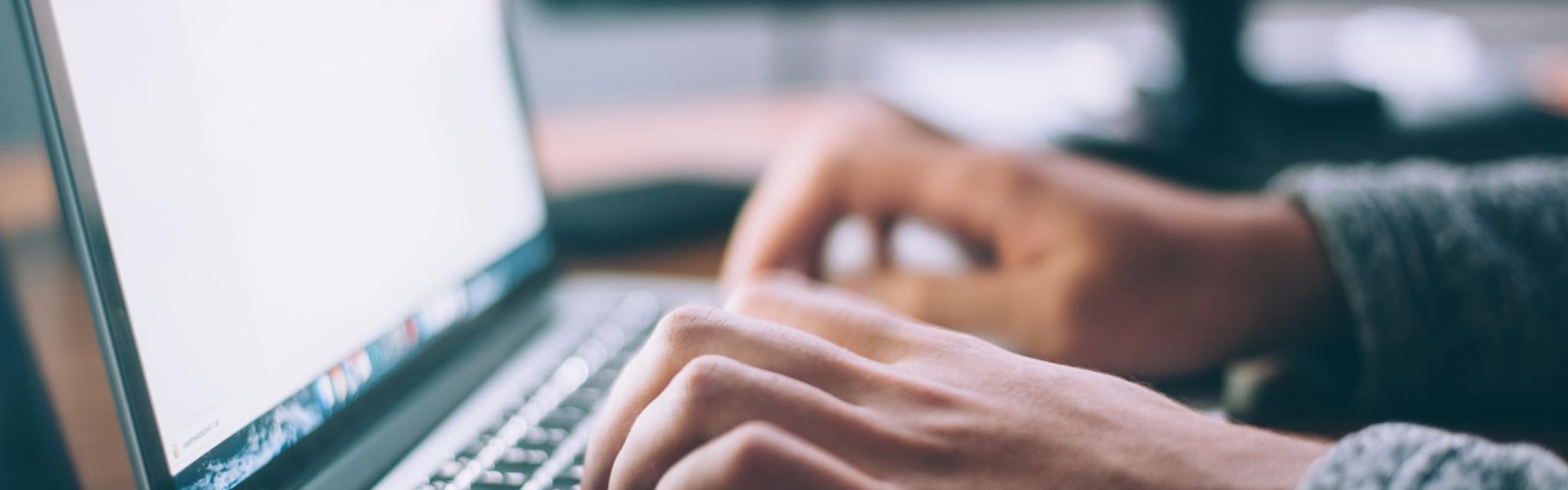
The common rail is a critical part in the common rail fuel injection system. As a pressurized fuel accumulator, it has to endure harsh operating conditions which causes material fatigue. If not resisted, the material fatigue damages the common rail and it breaks much earlier than expected. The most reliable common rails counter the material fatigue thanks to their fatigue resisting mechanical properties against internal pressure, vibration, cavitational, corrosion and surface flawing fatigue. There are three crucial process contributing to the perfect creation of a strong, reliable and high-resistant common rail:
The wise selection of the raw material
The design that considers every single manufacturing step and anticipates possible problems
The forging manufacturing process
The aggregation of these three factors deliver best resistance against the following problems:
Internal Pressure Fatigue on Common Rails
Current Common Rails handle rapid fuel pressure changes from start to stop, between stationary to idle to snap acceleration or deceleration on the ECU's request. This process is so fast that for instance it only lasts from when the acceleration pedal is pushed until the driver feels the acceleration itself. This obviously cause common rail's material fatigue and microscopic cracks eventually form.
The common rail must be manufactured with improved internal pressure fatigue resistance to counter fatigue-incurring effects of internal pressure changes. Materials as forged aluminum and forged stainless steel are preferred for common rails. Setforge provides also the best processes that improve the inner surface's strength and hardness even more.
Common Rail's Vibration Fatigue
Internal and external sources may contribute to the vibration fatigue of the common rail. Internally the common rail dampens pressure vibrations from the high pressure pump and the injection process. Externally the whole common rail system is vibrated by the engine environment which is moving because of the combustion power. These vibrations weaken parts, particularly joints to the fuel lines and fastening spots to the engine frame. Therefore, they start moving asynchronously. The emerged friction forms microscopic cracks on the surface of both components.
Since vibrations are inevitable in engines, the selected material should carry high initial vibration fatigue resistance while keeping up to dimensional requirements. The product design must incorporate vibration calculation of all the engine's components so that vibrations between them resonate harmonically. The manufacturing process design should include exact measures, especially in processing the areas of joints and fastening spots.
Cavitational Fatigue on Common Rails
As a fuel injection system, the common rail system is a flow system with low and high pressure areas. This condition supports cavitation within the system. The low-pressure area from the fuel tank to the fuel filter to the high-pressure pump is where bubbling begins. The high-pressure area from the high-pressure pump to the common rail and injectors into the combustion chamber is where the bubbles implode.
It's reasonable to manufacture the common rail with mechanical properties to counter cavitational fatigue because the nature of the common rail system itself supports cavitation. Setforge improves the cavitational fatigue resistance through design, detailled pre-production and forging, selected as the best manufacturing process.
The product design increases common rail's cavitational fatigue resistance by having a part to maintain residual pressure. Residual pressure will bridge the pressure gap between high- and low-pressure areas. This limits bubble formation and therefore, prevents cavitation. Pre-process analysis must also be done to identify areas prone to cavitation. The most common method is the Finite Element Method (FEM) analysis.
Corrosion Fatigue on Common Rails
The common rail's outer surface will corrode because it's in an exposed environment of the engine compartment. This environment doesn't inhibit airborne oxidant contact thus promotes oxidation. However the common rail's main task is to accumulate pressurized corrosive fuel. This creates an unexposed aqueous corrosive environment inside common rails and the inner surface will corrode by prolonged fuel contact. Corrosion gets worse by factors as microbes, fungi, and fuel contaminants. The common rail's outer surface corrosion damage degrades it's thickness and therefore crust flakes are created. The damage on the inner surface usually forms cracks on vulnerable areas like joints to the pipes and valves.
The best ways to improve the corrosion resistance of the common rail is reliable material selection and surface processing. The surface processing is usually a metal naturally forming passivation film that is made of a very thin layer of oxide covering the entire exposed surface preventing further oxidation. This process can also be stimulated by anodizing or by giving a chromate conversion coating. Other surface improvements include plating, painting and coating.
Surface Flawing Fatigue on Common Rails
Surface flawing are surface defects that result in homogeneity disruption (as gouges or scratches) or in chemical composition, structure or dimension deviations (as uneven chromium distribution on stainless steel surface). All these physical defects can occur on outer or inner surface where the most prone areas are the joints to the fuel lines. Inexact heading and upsetting parameters to give form to the joints especially curvature, angle and depth can create microscopic defects if not well set.
Surface flawing resistance should be improved through material selection and adequate design. The properties of the selected material should include: pre-manuacture strength, hardness, malleability and temperature endurance. Since those are needed to endure manufacturing without defecting, the process design should prioritize them. Each process parameters must be well set to avoid defects. For example careless heat-treatment can lead to the metal under- or over-responding to it and defecting. Surface flaws can be detected by investigating the metal's physical properties upon exposure to X rays; infrared, ultraviolet, and gamma rays; radio waves; ultrasonic vibrations; and magnetic and electrostatic fields.
Setforge considers every single phase of the common rail's production cycle. Our precise raw material selection secures all required fatigue resisting mechanical properties of the chosen material. The product and process design guarantee best performance of the common rail later and the forging manufacturing process completes the perfection of the final product.