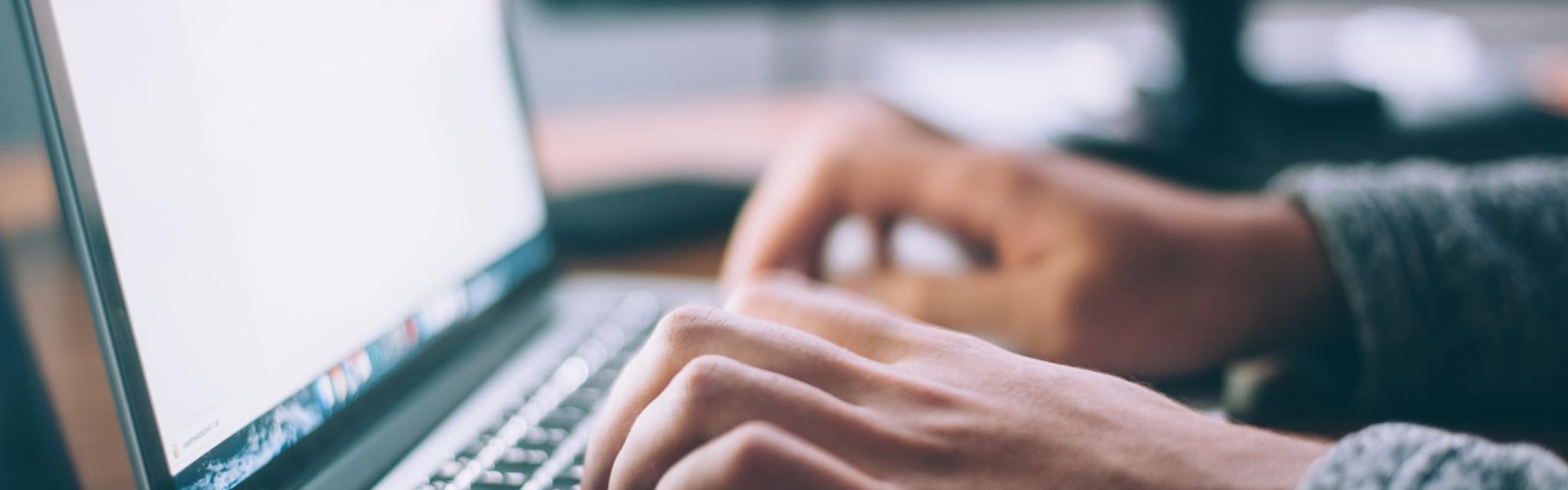
Today the majority of oil and gas OEMs are supplying the sector with fluid ends manufactured from one single block. This product features undoubted advantages but it is simply too expensive, too bulky and too prone to wear between the cavities. And since fluid ends are key components of the pressure pumps meant to maximize productivity in fracturing operations because of their durability and dependability, the sector is looking for emerging technologies for better maintaining and increasing the life of fluid ends.
Therefore, a small but solid group of key players have started the technological turn and opted for new materials and design in the manufacture of fluid ends for hydraulic fracturing. Shifting from mono to split blocks or modular design will drastically reduce the downtime of the pumping plants. Furthermore the new fluid end can be easily maintained and serviced directly at the workplace thanks to the availability of spare parts and the possibility for replacement of the damaged cavity. The service life of the part can be increased with a heat and carbide treatment if necessary.
Fluid ends are of critical importance for the pressure pumping industry and their failure may have dramatical impact on the final outcome. Subject to ext reme environments as pressure, chemicals and slickwater, fluid ends can fail in as little as 100 to 500 pumping hours.
This article discusses current designs of fluid ends compared to an innovative solution, aiming at introducing a solution to important industry’s problems as fluid end premature failure, environmental issues related to the performance of a fluid end and fracking performance.
What Are the Main Functions of a Fluid End?
A fluid end is situated in a fluid pump and contains the parts, which are directly involved in moving the fluid. The inlet and outlet of the fluid end are connected to a suction and discharge pulsation dampener. The inlet serves to create a vacuum, which enables the move of fluid from the reservoir into the inlet line. Then, the liquid is pushed out through the outlet into the hydraulic system. The fluid end and its components allow the high pressure injection of the fluid.
The movement of the piston changes the volume of the pump’s body. The pressure gets higher as flow progresses from the suction to discharge. The proper operation of a piston pump requires the presence of two valves or non-return valves: for admission (or aspiration) and for repression.
The movement of the piston causes:
- a depression in the upper compartment of the pump bod, which opens the valve on the suction side and closes the valve on the discharge side. The compartment fills up.
- an overpressure in the lower compartment of the pump body, which opens the check valve on the discharge side and closes the lower valve on the suction side. The compartment is empty.
What Causes the Fluid End Premature Failure?
There are several significant problems that can lead to the premature failure of the fluid end. Most of the following issues can be easily avoided during the design phase and through a different material choice.
Fatigue Cracking
Fatigue cracking depends on the endurance limit of the metals used for the manufacture of the fluid end. Also, some solutions have intersecting bores that begin to exceed their endurance limits when exposed to the pump pressure. Excessive cavitation and impact from foreign objects can create as well separations or cracks in the fluid end material.
Corrosion
The easily corroding carbon steel is contributing to cracks and damages. Also, the metal and iron contaminants found in well stimulation fluids can deteriorate the fluid end metal. Superior stainless steel is definitely the better material choice extending the pumping hours of the fluid end nearly 10 times with the proper maintenance.
Cavitation
Rapid changes in pressure lead to the forming and imploding of cavities in the liquid. An elaborated design can significantly reduce the appearance of this problem.
Washing Out
This issue is related to the fact that the valve seat is almost twice as hard as the surface of the fluid end. Valve seats are pulled out and changed in the field. There is often dirt and sand that can get trapped between the valve seat and the fluid end taper, leaving some damages that prevent the valve seat from sealing properly and leading to the washing out of the fluid end in this area.
What is the Common Design of Current Fluid Ends?
Most of the current fluid ends have a monoblock structure and are incorporated into triplex (with 3 pressure plungers) or quintuplex (with 5 pressure plungers). These units are operating sometimes at 300 strokes per minute and this often results in fatigue cracking of the fluid end, benefited as well by the current monoblock design of the component.
Fluid end developments and modular design prolong fluid end life while maintaining higher pressures.
The Setforge /Technogenia Single Block Solution for a Better Fluid End Performance
Considering all these difficulties and the necessity of the sector of well service capabilities at increasing depths, Setforge and Technogenia have combined expertise to launch a unique product. The new solution is designed to survive harsh operating environmental conditions, while performing at increasingly high pressures and high flow rates.
The Setforge /Technogenia fluid end is made of stainless steel to provide increased durability and reduce erosion by resisting fatigue cracking. The solution is improving as well pressure cycles and reducing cylinder stress due to the natural break in the stress transfer. The single block fluid end was closed-die forged with a near-net shape to minimize machining, which increases the endurance limits of the intersecting bore.
After forging, the wear zone of the product was submitted to a special anti-wear protection for a top hardness. The LaserCarb technology is adding an anti-abrasion material to the wear parts through a laser beam melting the deposition powder directly on the part. The new fluid end approach is aiming as well at minimizing the machining part of the manufacturing process as much as possible.
Benefits of the Setforge/ Technogenia Fluid End at a Glance:
- Easy maintenance for reduced downtimes;
- The replacement of monoblock assemblies with modular fluid ends doesn’t require any additional tools or trainings;
- Minimized flexing stress amplitude for improved pressure cycles;
- Reduced spare parts costs;
- Stamping results in cost reduction compared to free forging since there is 30% material less;
- Specific material flow for improved fatigue resistance;
- Weight reduction;
- Minimized machining and utilization of smaller machining machines and thus reducing the cost of machining;
- Possibility of using steel instead of stainless steel for similar performance levels.
Fluid ends are components that can easily fail because of a fatigue cracking or a reaction to chemicals, erosion or a combination of all these. The fluid ends with a new design and manufactured from a split block are slowly replacing the common monoblock structures to improve maintenance, reduce downtime and provide more practical inventory options. It is far easier to stock single block fluid ends and replace them fast when needed instead of dealing with laborious installation of a bulky monoblock assembly.
As trusted partners of the oil and gas industry, Setforge and Technogenia are aware of the sector’s challenges and are committed to delivering most reliable solutions.