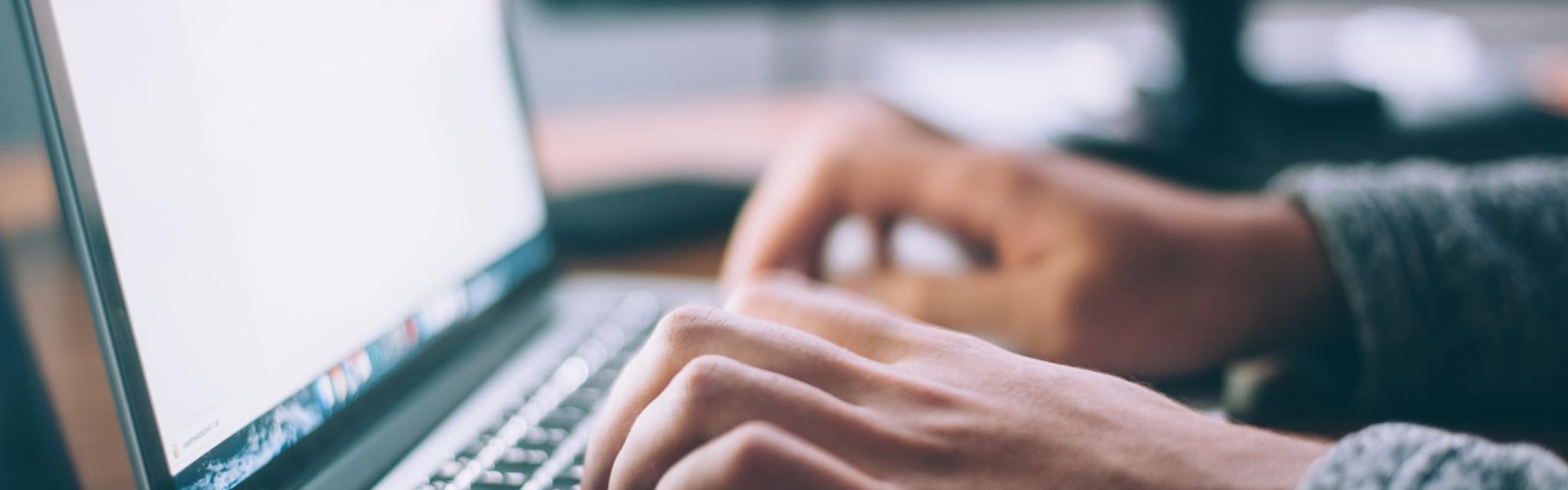
The common rail is the most essential component of the direct fuel injection system. Eventual common rail failure is always critical since the entire vehicle can be blocked or even set on fire. Most common rail problems are related to the complex geometry of the components and possible cracks caused by material fatigue or during the manufacturing process. Therefore a special attention should be paid to the following:
Define and Keep Best Parameters
Less fuel consumption, less fuel emissions, safer performance for high comfort are only some of the improved characteristics of the today’s vehicles. Automotive manufacturers are in continuous development of better automotive solutions in order to improve not just the cars or trucks but also our life quality. Petrol and diesel engines have been entirely modified in the last years. Size and weight have been minimized, therefore material and design optimized.
As the most important component in the direct fuel injection system, the common rail was also adapted to the new requirements. Its geometry has become much more complex. Geometry mistakes can easily lead to irreversible common rail problems and damage of the components. The precise parameters should be defined in the design phase and strictly followed during the forging, trimming and cooling process. This requires expertise and best tools.
Select Best Metal
The common rail itself acts as a common fuel storing rail and it is permanently exposed to heat and pressure. Therefore, if the raw materials haven't been selected wisely, quality problems can occur. The most common rail problems related to material selection are shorter product life and reduced fuel accumulation volume:
Shorter product life means that the common rail will break sooner than expected especially if it has been made of a material with low resistance to conditions that cause fatigue and wear. Those conditions include cyclic loading/unloading, constant high operating internal pressure, and the fuel's cavitational implosions. Fatigue and wear eventually make the material fail or crack. By selecting materials that combine in the best way strength and hardness, leakage and breakage will be avoided and product's fatigue life will be prolonged.
The other important common rail problem related to material selection is the reduced fuel accumulation volume due to uneven hardness of the selected metal. In order to develop better rigidity, the metal should be heat treated and hot forged. The imbalanced distribution of grain structure leads to non-uniform volume of diesel along the pipe, affecting the injections. They start injecting not the correct fuel amount to each cylinder heads on each injection event. Different combustion events have also unequal and deviated volumes of injected fuel.
Choosing a common rail material with uniform heat-treatment response and the right and evenly distributed section thickness and rigidity, has been proven as the best way to secure the exact pressurized fuel volume capacity.
Setforge possesses an excellent expertise in providing better design for a perfect common rail performance, adapted to the requirements of the client. We work in close collaboration with experienced steel makers to provide high-quality materials, developed to resist high fuel pressure and heat. Our common rails for gasoline and diesel engines are one piece hot forged components which eliminates any risk for possible cracks or leakages. As a trusted and longstanding partner of the automotive industry we know how to avoid all possible common rail problems. Our team of capable engineers takes always the most accurate decisions today in order to secure perfection tomorrow.