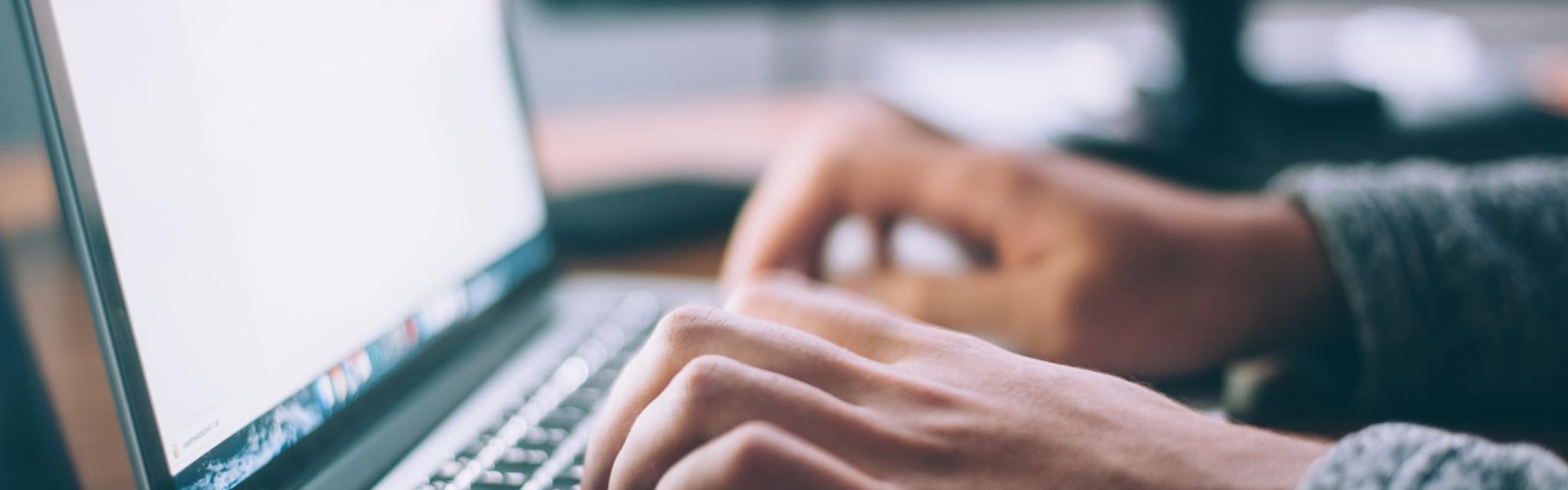
The Setforge-Technogenia Fluid End Offers Hydraulic Fracturing Reliability and Cost Efficiency
Hydraulic fracturing or, as it is commonly called fracking has made inaccessible oil and natural gas sources in tight geologic formations easier to reach and thus gave countries a greater energy independence. The technique represents a horizontal directional drilling combined with water, sand and chemicals at high pressure to fracture rocks. There are hydrocarbons released during the process.
Despite its success and highly appreciated economical gain, fracking has recently become quite controversial in an environmental context. One of the main concerns involves the huge amount of water that should be used, which is 100 times more than with traditional extraction methods. Other concerns are related to the possible contamination of ground water and surface pollution.
The industry professionals emphasize that pollution is usually the result of bad practice and could be easily prevented by experienced workforce and better solutions. Therefore the sector is in a constant search of innovative and highly reliable products.
What Is Hydraulic Fracturing and How Does It Work?
Hydraulic Fracturing is an oil and gas well development process used to create fractures in the rock and as well increase the size, extent, and connectivity of existing ones. The technique is usually performed by injecting water, sand and chemicals under high pressure into low –permeability rocks (as sandstone, shale and some coal beds).
The term fracking refers to how the rock is fractured apart by the high-pressure mixture. Natural gas or oil is released through the formed fissures and is drawn back up the well to the surface where it can be collected, processed and refined.
The conventional hydraulic fracturing in vertical wells has been used for over 50 years to improve the flow of oil and gas from common reservoirs. The current practice of horizontal drilling was introduced in the 1980’s and has continued to evolve.
Given the complexity of the process and the possible environmental concerns, the market is in a constant search of innovative, durable solutions.
A Single Block Fluid End for a Better Fracking Performance
The fluid end is one of the most critical components of the pressure pumping industry. Exposed to the constant pressure of water and chemicals, and the extreme environments of the fracking process, the fluid end can easily fail if it is not properly manufactured and maintained. Fluid ends can be as well one of the biggest concerns in terms of performance and cost for fracking companies when they fail permanently. Given the industry’s fast paced development and high competition, saving money and increasing profitability and productivity are main objectives.
One of the most common reasons for a fluid end to fail is fatigue cracking due to the metal fatigue and corrosion. This challenge can be overcome through an advanced geometry design and the choice of a top-quality, high-strength stainless steel. Furthermore, cracks in stainless fluid ends are found more frequently in welded areas than in non-welded areas. Therefore one-block solutions are preferable.
Setforge and Technogenia – 2 European companies, leaders in their respective fields – forging and anti-wear protection combined their know-how to design and manufacture an innovative fluid end solution able to face the sector’s challenges.
The product represents a single block fluid end with premium anti-wear protection for increased asset’s lifetime and improved pump efficiency. The fluid end was closed-die forged with a near-net shape to minimize machining, which increases the endurance limits of the intersecting bore. After forging, the wear zone of the component is submitted to a specific laser cladding (lasercarb technology). The LaserCarb process is a hard surfacing process that adds an anti abrasion material to the wear parts. The process consists of using the energy of a laser beam to melt the deposition powder on the part. A weld occurs between the deposit and the base material.
Emerging technologies for maintaining and increasing the life of fluid ends are of a critical importance for the successful functioning of the sector in the future. Investing in new materials and designs can drastically extend the life of the fluid end to upwards of 1,000 to 5,000 hours.
Advantages of the Setforge - Technogenia Innovative Single Block Solution at a Glance
- Improved installation shutdown times, with rapid change of pump bodies damaged;
- Cost-efficiency thanks to the optimized geometry and reduced machining cost;
- Better pumping efficiency, which improves the hardness and extends the lifespan;
- Increased life span with the less wear thanks to the LaserCarb technology;
- Better resistance and minimized fatigue failure due to premium materials.
Today, hydraulic fracturing is one of the most important techniques to bring petroleum oil hydrocarbons to the surface. The technique has a huge impact on the amount of produced oil and natural gas, especially in the U.S. The increased production has significantly lowered energy prices and carbon dioxide emissions by displacing coal in electricity generation. Despite these benefits, all professionals are aware of the controversial impact of the technique on the environment and therefore are continuously investing in innovative solutions and reliable equipment maintenance techniques.
As a trusted partner of the oil and gas industry, Setforge L’Horme is aware of the sector’s challenges and is committed to delivering most reliable solutions.